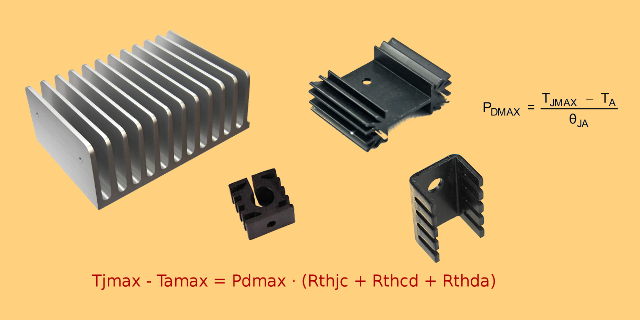
Un dissipatore è un corpo capace di trasferire all’ambiente circostante una quantità di energia termica applicata alla sua superficie. Con alcuni calcoli matematici la progettazione di un buon dissipatore di calore è una operazione abbastanza semplice. Vediamo quindi come progettare un dissipatore di calore applicando e spiegando delle semplici formule e poi con degli esempi pratici.
ATTENZIONE: quello che hai appena letto è solo un estratto, l'Articolo Tecnico completo è composto da ben 1016 parole ed è riservato agli ABBONATI. Con l'Abbonamento avrai anche accesso a tutti gli altri Articoli Tecnici che potrai leggere in formato PDF per un anno. ABBONATI ORA, è semplice e sicuro.
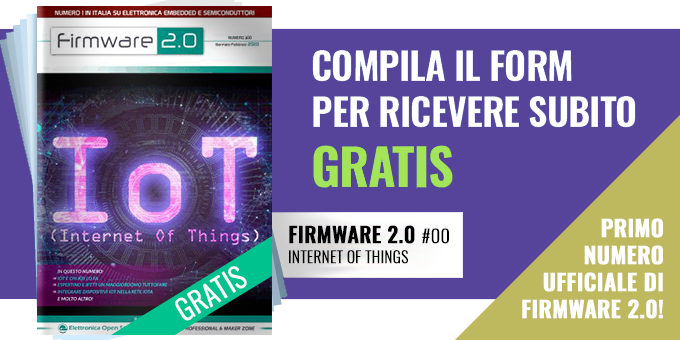
Le nuove frontiere della tecnologia stanno portando alla scomparsa dei pesanti dissipatori, come del resto anche dei pesanti trasformatori. RDSon sempre più basse, Ultra Low Drop Out e case sempre più rivolti alla dissipazione diretta sul pcb ne sono un esempio. Anche il diffondersi dei circuiti a commutazione del resto. Nei circuiti stampati anche abbiamo soluzioni per dissipare ad esempio in alluminio, molto utilizzati nell’illuminazione a led.
Però tanto prima o poi ci si trova davanti alla necessità di un bel radiatore…..
esatto…
La necessità di “di un bel radiatore” finisce per essere assolutamente innegabile…
Certamente la dissipazione del calore è il più grande problema da cui è affetta la tecnologia allo stato solido…
Da questo punto di vista, spero davvero nell’utilizzo dei superconduttori 🙂
un articolo molto utile ed efficace.
Complimenti.
mi associo questi commenti. Complimenti davvero.
Anche gli esempi sono davvero chiari ed utili.
scusate, ovviamente manca una “a” 🙂
Articolo sempre utile. Ho apprezzato molto i 3 esempi pratici che chiarificano immediatamente come calcolare il dissipatore, per i “non addetti” 🙂
Terrei però a precisare che la foruma della resistenza termica Rth o RTD (che dir si voglia) è arrotondata. E’ stato eliminato il parametro relativo al trasferimento di calore dalla giunzione al case e dal case all’esterno. Direi che in alcuni casi è possibile trascurare questo valore, in altri invece sarebbe bene tenerne conto:
Rth= (T1 – T2)/Pd – (RTJC + RTCD)
RTJC è la resistenza che il calore incontra a passare dalla giunzione al case ed ovviamente dipende dal case ( questo valore si trova sul datasheet)
RTCD è la resistenza che il calore trova nel passare dal case all’esterno, quindi al dissipatore e dipende da vari fattori, come dal tipo di case, dal contatto diretto, oppure con mica e dall’utilizzo del silicone. Esistono tabelle apposite relativamente ai vari case.
vorrei sottolineare un aspetto importante, peraltro correttamente riportato nell’articolo, e cioè l’uso della ‘pasta termoconduttiva’… tutti i ‘conti’ vanno a ‘pallino’ se la superficie di contatto non è sfruttata totalmente.
sì, hai ragione.
È molto importante!
Io imparai, all’epoca della prima esperienza nell’assemblare un computer, quanto fosse importante. Fortunatamente, senza fare danni 🙂
La formula per calcolare la resistenza termica non tiene conto delle alette di raffreddamento.
In che maniera queste influiscono? C’è una qualche formula per tenere conto dell’altezza delle alette, distanza tra le alette, ecc ?
Oppure il loro contributo è trascurabile rispetto alla dimensioni del blocco?
Qui c’è qualche formula:
http://pcfarina.eng.unipr.it/dispense01/altamura132421/altamura132421.htm
grazie!
Non sono convinto della formula Rth = r x A:S o perlomeno della sua interpretazione, secondo me è come per la resistenza elettrica ovvero resistività (termica) per lunghezza (spessore) diviso la sezione attraversata dal flusso termico, In questo modo tornano anche le unità di misura °C/W=°C.cm/W x cm : cmq. Questa formula tra l’altro da la resistenza termica del metallo (piccola) ma il grosso della resistenza termica è nel passaggio tra dissipatore ed aria.