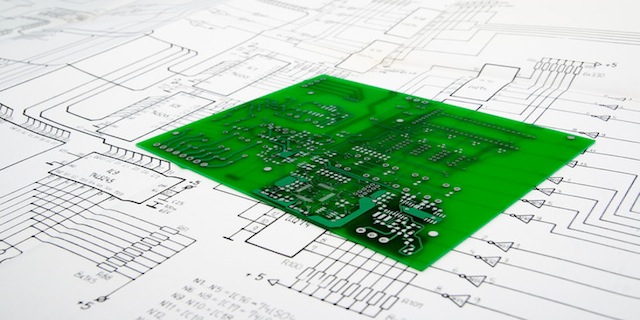
In questa ultima parte del corso sullo sbroglio dei circuiti stampati vedremo alcuni esempi pratici supportati da immagini di applicazioni reali. Ben 14 differenti suggerimenti e trucchi per realizzare ed ottimizzare il vostro circuito stampato. Dalla gestione dei quarzi a quella dei vias, dallo spessore del rame agli stub, dalla dissipazione agli isolamenti ed a tante altre soluzioni, tutte in un contesto armonioso e gradevole alla vista, perché ormai è noto, un circuito bello da vedere è quasi sempre un circuito ben funzionante!
ATTENZIONE: quello che hai appena letto è solo un estratto, l'Articolo Tecnico completo è composto da ben 2588 parole ed è riservato agli ABBONATI. Con l'Abbonamento avrai anche accesso a tutti gli altri Articoli Tecnici che potrai leggere in formato PDF per un anno. ABBONATI ORA, è semplice e sicuro.
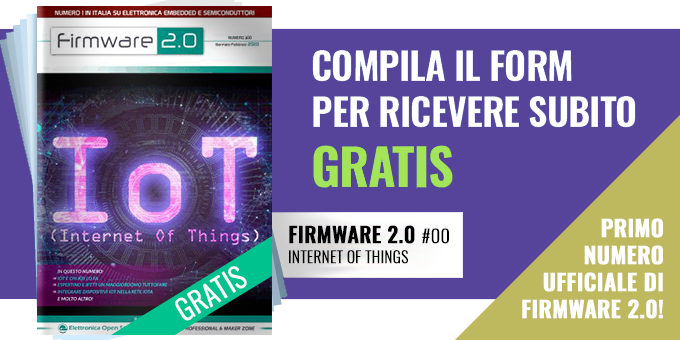
Quella sugli STUB è un’indicazione molto utile.
Non saprei dire quante volte ho sbagliato i primi tempi!
Scusate, una domanda sull’accendigas…
Io non ho capito: se non è un metodo “convenzionale”, perchè leggo che i risultati sono soddisfacenti?
Cioè, saranno anche accettabili ma resto il problema di dover comunque controllare con attrezzi “canoninci” o standard, giusto?
Oppure ho capito male?
L’errore classico è il testpoint 🙂
Comunque se i segnali non sono critici (hi-speed) non ci sono problemi, anche se a mio avviso è sempre meglio evitarli, anche per motivi apparentemente banali, ma che in produzioni di volumi elevati, possono incidere negativamente, come ad esempio la rottura (o micro-danneggiamento) della pista. Considerate sempre che uno stub introduce un angolo retto e quindi in particolari condizioni potrebbe essere a rischio.
I risultati SONO soddisfacenti ma non è certo un metodo “convenzionale.”
Ovviamente se si deve certificare il prodotto, si dovrà ricorrere ad un laboratorio specifico, ma, fermo restando che in alcuni casi ci si potrebbe anche prendere la responsabilità, questo sistema è un valido pre-test.
Immaginate di riscontrare un problema durante le prove di laboratorio, dove state pagando (spesso profumatamente) l’affitto del sito (con strumentazione e manodopera) e magari anche una trasferta al personale.
Non sarebbe meglio arrivare in certificazione con una quasi certezza di superare la prova ESD?
Senza ovviamente spendere una fortuna per acquistare una ESD-Gun “convenzionale” 😉
Nooooooooooooo…
Già finito?!?! 🙁
Complimenti a tutti!
Davvero una lettura interessante.
Scusate se lo chiedo ma ci sarà un volume monografico su PCB ART?
Sarebbe comodo averne uno, visto che ci sono articoli “sparsi” in tutti i numeri usciti finora 😀
Mi accodo anche io a questa richiesta! 🙂
E comunque complimenti a tutti! Bravissimi, come sempre!
“Tutto quello che ha un inizio, ha una fine” 😉
Complimenti davvero!
Aspetto con ansia di poter scaricare la monografia.
Quando sarà pronta?
Ti/Vi terremo aggiornati 🙂
Continua/continuate a seguirci 🙂
Sono inesperto e non mi è chiaro il paragrafo “#7 Scaricate i piani”.
Se ho capito bene c’è la possibilità che il solder mask, la “verniciatura” tipicamente verde, non venga dello stesso spessore su tutto il PCB ma non capisco che problemi ciò potrebbe dare.