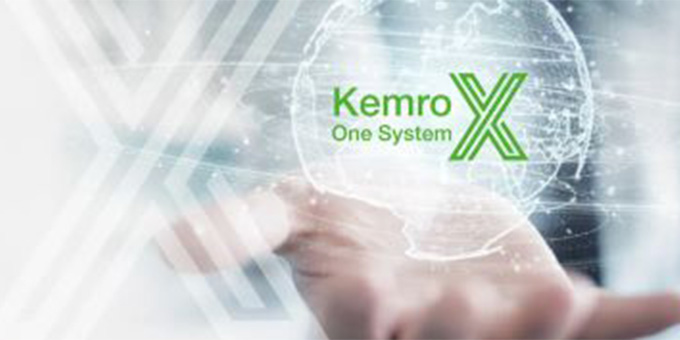
Nell'ambito della trasmissione robotica, la calibrazione e la compensazione degli errori sono essenziali per garantire il corretto funzionamento dei robot. Tuttavia, questo processo è complesso e presenta numerose problematiche dovute a vari fattori applicativi. In questo articolo, esploreremo le principali sfide legate alle giunzioni e agli ingranaggi dei robot, con un focus su alcuni aspetti spesso trascurati ma significativi.
La geometria di un robot è definita dagli angoli e dalle distanze tra le giunzioni delle diverse parti che costituiscono il braccio. Il Tool Center Point (TCP), ovvero il punto di riferimento dello strumento utilizzato, cruciale per la calibrazione e la compensazione, influenza sia il posizionamento che l'orientamento del braccio. In un sistema con cinematica seriale, gli errori angolari e delle giunzioni si sommano, incrementando l'errore complessivo del TCP. Di conseguenza, errori nelle distanze si traducono direttamente in errori del TCP, mentre le discrepanze angolari influiscono tramite la leva fisica relativa al centro di rotazione del braccio.
Caratteristiche degli ingranaggi: rigidità, elasticità, isteresi, giochi e ripple
I controller per robot industriali lavorano generalmente attraverso modelli rigidi, ignorando fattori di flessione o deformazione. Nella realtà, la struttura del robot e gli ingranaggi non sono perfettamente rigidi, la posizione delle giunzioni, e quindi del TCP, può variare a seconda delle forze applicate. L'elasticità degli ingranaggi, che in pratica è una deformazione dipendente dal carico applicato, diventa pertanto un fattore cruciale. Considerato che i cuscinetti e le giunzioni del robot presentano livelli di elasticità, con variazioni a seconda del carico, occorre tenere presente anche che l’effetto non è costante: gli ingranaggi tendono ad essere più morbidi a carichi bassi e più rigidi con carichi crescenti. A questo punto, un modello dinamico accurato del robot può compensare questi effetti, migliorando la precisione complessiva.
In fase di progettazione, è essenziale considerare l'elasticità degli ingranaggi, poiché le giunzioni sono punti determinanti e devono essere progettate per avere caratteristiche simili a quelle degli ingranaggi e dei cuscinetti in modo da mantenere una struttura bilanciata. Ad esempio, una giunzione elastica può influire sulla precisione del TCP, specialmente se le forze applicate variano lungo il percorso del robot. Pertanto, l'elasticità degli ingranaggi deve essere incorporata nei modelli dinamici per calcolare l'offset in base al carico di coppia e compensarlo adeguatamente. Questa compensazione diventa meno efficace se il valore di carico è costante, la superficie di lavoro è contenuta e le dinamiche non sono elevate. Tuttavia, effettuando misurazioni dell'intero robot e adattando i parametri dell'ingranaggio, è possibile limitare gli effetti dell'elasticità delle giunzioni.
L'isteresi rappresenta il ritardo di un ingranaggio nel rispondere alle sollecitazioni, in correlazione al suo stato precedente. Questo fenomeno, insieme all'elasticità e al gioco degli ingranaggi, complica ulteriormente la determinazione precisa della posizione delle giunzioni. L'isteresi provoca deformazioni elastiche che non tornano ai valori iniziali a causa dell'attrito, generando offset correlati ai cambi di direzione del carico. I modelli che riguardano il gioco, utilizzati per macchine a controllo numerico, aggiungono il parametro di isteresi in base alla direzione del movimento, ma rappresentano solo una semplificazione approssimativa. Ad esempio, durante i movimenti lenti, con angoli prossimi allo zero, è difficile determinare l'esatta posizione della giunzione a causa della presenza di gioco. Ciò crea incertezze sulla posizione reale ed effettiva della giunzione, influenzando negativamente la precisione del TCP. Gli ingranaggi, infatti, non tornano mai alla posizione iniziale dopo un movimento a causa della combinazione di elasticità e attrito. Questo problema è amplificato dai giochi tra gli ingranaggi, che creano ulteriori incertezze sulla posizione. In pratica, l'effetto dell'isteresi può causare errori significativi nel posizionamento del robot, compromettendone la precisione. Come per l’elasticità, anche la gestione accurata dell'isteresi è fondamentale per mantenere la precisione del robot.
Il ripple è un'altra caratteristica importante degli ingranaggi, dovuta alla variabilità del rapporto di trasmissione che è condizionata dalla geometria dei denti e dalle tolleranze di produzione. Questa variabilità può causare scostamenti nella posizione del TCP con valori che possono superare il decimo di millimetro sui robot di medie dimensioni. Sebbene progettati con modelli geometrici simili, gli ingranaggi possono presentare variazioni nel rapporto di trasmissione a causa di differenze nella profondità dei denti e nel rapporto tra i raggi a livello del punto di contatto. Sebbene tutte queste variazioni possano risultare estremamente piccole, sono in grado di impattare significativamente sulla precisione del robot, specialmente se si prendono in considerazione applicazioni che richiedono alta precisione.
Errori del Servo e Attrito
Durante il funzionamento, può verificarsi un offset tra la posizione effettiva del motore e i valori impostati, variabile dovuta anch’essa al carico e alle forze esterne. Questo errore deve essere tenuto in considerazione per mantenere la precisione del robot. L'attrito a bassa velocità, localizzato in particolare nei punti di inversione degli assi, rappresenta un problema significativo per l’alta precisione. Per un robot che opera nello spazio libero senza contatti, un modello dinamico accurato può teoricamente eliminare questi errori, mantenendo il robot in assetto con coppie determinate senza necessità di feedback. Tuttavia, nella pratica, sebbene si disponga di un modello dinamico accurato, i controlli continuativi di feedback sono essenziali per compensare gli errori del modello e mantenere la precisione del robot.
Soluzioni per la compensazione degli errori
Per eliminare gli effetti problematici degli ingranaggi, esistono due principali approcci: il sistema a doppio encoder e la soluzione KEBA.
Sistema a doppio encoder: consiste in un secondo encoder sull'albero di uscita dell'ingranaggio che misura l'angolo della giunzione. Il doppio encoder consente di ottenere una misura precisa dell'angolo della giunzione, indipendentemente dalle problematiche degli ingranaggi. Ad esempio, se il loop di controllo della posizione include un integratore per portare l'errore di posizione a valore zero, il secondo encoder permette di tenere conto dei giochi e dell'attrito, migliorando la precisione complessiva del robot. Questo sistema può attenuare gli effetti negativi, fornendo al controller di movimento informazioni accurate.
Soluzione KEBA: KEBA, in collaborazione con Nabtesco, azienda specializzata nella produzione di ingranaggi cicloidali, riduttori, sensori angolari ed encoder specifici per il settore della robotica, ha sviluppato una piattaforma che integra le problematiche degli ingranaggi fin qui analizzate già in fase progettuale. La piattaforma Kemro X permette l'analisi, la simulazione, il controllo e la calibrazione dei robot, con modelli dinamici e funzioni integrate che considerano tutti i parametri rilevanti. Attraverso la soluzione KEBA, è possibile inserire i dati specifici di ogni ingranaggio nel modello del robot, ottimizzandone la precisione come anche eseguire un processo di validazione accurato, migliorando la progettazione e l'implementazione dei robot.
La Piattaforma KEBA Kemro X
Kemro X è una soluzione hardware e software che supporta la validazione dei robot secondo lo standard ISO 9823. A livello hardware, comprende CPU di controllo e di sicurezza scalabili in grado di gestire programmi PLC, Motion e multi-robot, HMI da pannello e palmare, drive multi-asse compatti ed efficienti, e una gamma di servomotori. Il software offre funzioni avanzate per l'analisi e la calibrazione, migliorando significativamente la precisione dei movimenti robotici. Kemro X consente di integrare vari aspetti critici della progettazione e dell'operatività dei robot. Le CPU di controllo e di sicurezza scalabili permettono di adattare il sistema alle specifiche esigenze applicative, mentre gli HMI offrono un'interfaccia utente intuitiva e versatile. I drive multi-asse, compatti ed efficienti, supportano un'ampia gamma di servomotori, migliorando la flessibilità e l'efficienza del sistema.
Conclusioni
Come abbiamo visto, la precisione dei robot è influenzata da vari fattori. Soluzioni come il sistema a doppio encoder e la piattaforma KEBA Kemro X rappresentano approcci differenti ma che possono offrire strategie avanzate per la compensazione degli errori. Con l’implementazione dei robot che, in misura crescente, assolvono a operazioni ad alta precisione, abbiamo potuto constatare come la corretta calibrazione si traduce nell’aumento di efficienza delle applicazioni robotiche industriali.
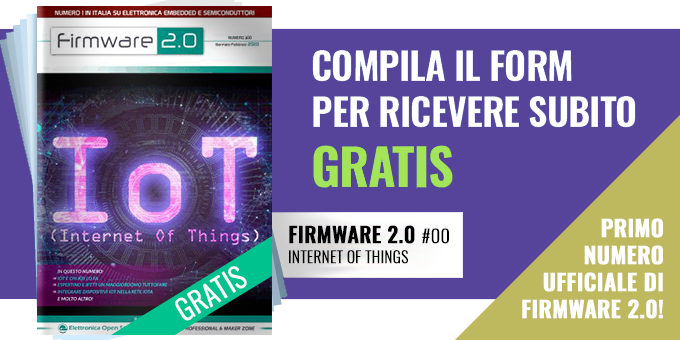