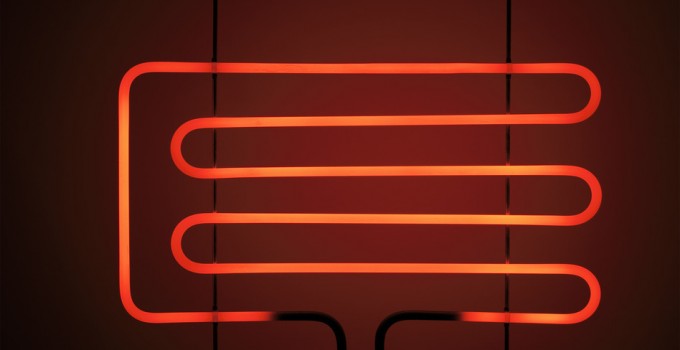
Per le aziende che utilizzano componenti elettronici, il problema della dissipazione del calore sta assumendo connotati importanti. In particolare nelle TLC e soprattutto in questo momento storico, in cui i governi di tutto il mondo fanno pressione sulle aziende per ridurre questo e altri fattori e creare così prodotti “green”.
La dissipazione del calore nei componenti elettronici
Il problema della dissipazione del calore nei componenti elettronici può essere affrontato sia dal punto di vista della componentistica (elettronica) che da quello dell'architettura stessa dei sistemi elettronici. Il mercato è caratterizzato da due soggetti forti. Da un lato ci sono i venditori di dispositivi elettronici basati sul silicio che ricercano di continuo soluzioni tecnologiche avanzate che permettano un minore consumo di potenza (e quindi una riduzione del calore dissipato). Dall'altro abbiamo le OEM (original equipment manufacturer) che sono tutte quelle compagnie che rivendono tali prodotti e portano avanti di fatto un approccio diverso, come quello della realizzazione di nuovi e più efficaci sistemi di raffreddamento.
Da un punto di vista tecnologico, una minore dissipazione di calore si è ottenuta miniaturizzando i dispositivi. Riducendo le dimensioni dei transistor, dei capacitori e dei resistori integrati si è potuto inserire nello stesso chip un numero di componenti elettronici maggiore, incrementando da un lato la capacità computazionale del chip e riducendo dall'altro l'assorbimento di potenza. Questo tipo di approccio ha, comunque, dimostrato di avere un grosso limite.
Oltre un certo grado di miniaturizzazione (tecnologia a 90 nm) non è più conveniente andare, a causa di alcuni fenomeni che avvengono all'interno del dispositivo stesso. Tra questi nei componenti elettronici, ricordiamo le correnti di leakage, che attraversano il transistor e causano una dispersione di potenza e una conseguente riduzione delle prestazioni del dispositivo stesso. Per risolvere il problema delle correnti di leakage, gli step successivi di progetto da parte dell'industri elettronica sono stati quelli di realizzare package con caratteristiche migliori e di utilizzare tecniche di coupling (il collegamento fisico tra il chip e la scheda) diretto.
Le soluzioni al problema della dissipazione del calore nei componenti elettronici sono state nel tempo diverse. Uno degli approcci più utilizzati è stato quello del raffreddamento ad aria. Il progetto di questi sistemi è legato al dimensionamento dello chassis, alla direzione dell'aria, al dimensionamento delle ventole. Uno dei primi esempi di standardizzazione di queste tecniche è il VMEbus, progettato quasi trent'anni fa da Motorola. Sulla stessa scia, il processo manufatturiero odierno si basa sull'ACTA, che sta per Advanced Telecommunications Computing Architecture. Queste tecniche di progettazione mirano alla diminuzione della temperatura. Un approccio passivo, certo, ma efficace.
Un recente documento (ICD, Interoperability Compliance Document) della CP-TA (Communications Platforms Trade Association) ha incluso un certo numero di profili termici validi per le aziende. Tali profili si basano sulla misura dei parametri fondamentali di potenza che permettono alle OEM di comparare le performance dei vari sistemi e di inserire questi in diverse categorie in funzione degli stessi parametri misurati. In pratica, l'ICD non è altro che una semplificazione dei precedenti ETSI, NEBS e NEDS (che sono standard di progetto in uso).
La Texas Instruments ha realizzato alcune prove utilizzando tre di questi profili. Nel primo di questi, 32 componenti (operanti a una potenza massima di 4 watt) sono stati disposti su una scheda grande 280X170 mm secondo righe e colonne senza alcuna tecnica di riduzione della temperatura. Nel secondo profilo è stato utilizzata una tecnica di raffreddamento della scheda. Nel terzo, è stata implementata una soluzione per mantenere la temperatura di giunzione (105°C) stabile.
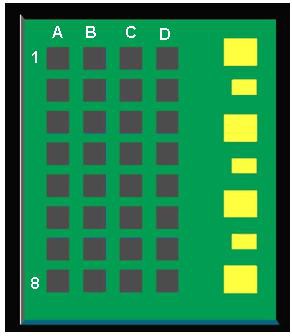
Nel primo caso, solo due componenti sono rientrati nel range consentito (105°C), mentre tutti gli altri lo hanno abbondantemente superato fino a una temperatura di giunzione di 150°C.
Gli stessi 32 componenti sono stati usati in un altro scenario. Tutti i componenti elettronici (disposti allo stesso modo) sono stati coperti da uno strato di alluminio anodizzato spesso 1mm. Tutti i componenti, in questo caso, sono rimasti al di sotto della temperatura di giunzione fissata. Pur tuttavia, se la temperatura di giunzione richiesta fosse stata di 90°C anziché di 105°C, solo alcuni componenti sarebbero “passati”.
Per il terzo profilo è stata utilizzata una tecnica più “verde” e più efficiente. Nei primi due profili lo spacing tra tutti i dispositivi era identico. In questa nuova prova, i dispositivi sono stati disposti nella scheda a distanze non uniformi, e come materiale per il sistema di raffreddamento è stato utilizzato rame puro. Il risultato è stato quello mostrato nella figura seguente, in cui la maggiorparte dei dispositivi si è mantenuto a una temperatura di giunzione ben inferiore ai 90°C.
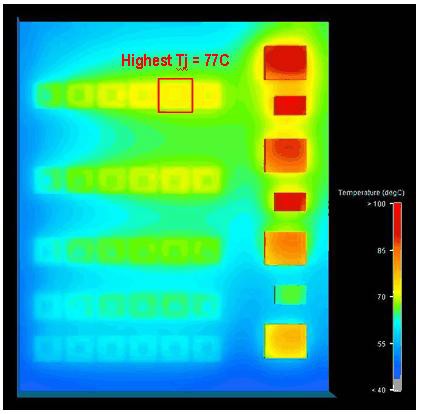
Questo studio ha dimostrato che una distribuzione simmetrica dei dispositivi su una board non è efficiente dal punto di vista della diminuzione della temperatura. Al contrario, una distribuzione dei componenti non simmetrica (e possibilmente su entrambi i lati della scheda) permette di ottenere profili termici migliori e quindi una minore maggiore dissipazione di calore.
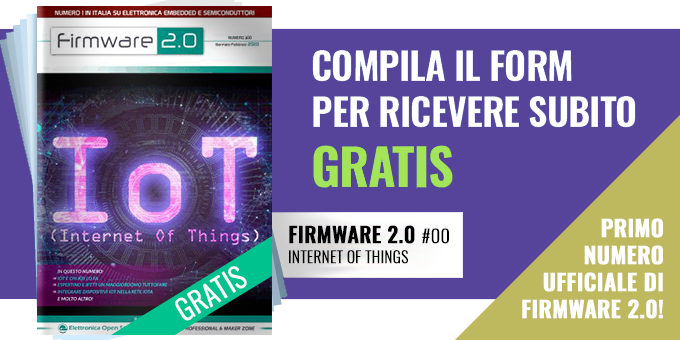
Al termine dell’articolo c’è un errore! “minore” andrebbe sostituito con “maggiore”.
Grazie di averci segnalato il refuso!
Ottimo articolo, argomento di cui sarebbe sempre opportuno parlare di piú, perché il raffreddamento adeguato sta alla base di un sistema elettronico/meccanico in grado di funzionare a dovere e in modo affidabile…
Mi rivolgo all’autore: perché non parlare anche, magari in un altro articolo, delle tecniche di raffreddamento a liquido per sistemi elettronici? =)
concordo pienamente con Fabrizio sia sulla qualità dell’articolo che sulla richiesta.. tempo fa, lessi su un altro sito una soluzione a liquido molto interessante: al posto di usare waterblock o cose simili, tutte le schede con i propri dissipatori passivi (nell’esempio era una server farm) erano immerse all’interno di una sostanza non conduttiva in vasche/reck.. Ciò aumentava notevolmente la capacità dissipativa e il consumo della struttura era notevolmente ridotto rispetto i tradizionali sistemi a liquido o aria.
Altro argomento utile sarebbe l’uso di celle di perltier con cui ricavare energia dal calore..
Su questo blog puoi trovare qualche esempio di utilizzo delle celle di peltier per produrre energia:
Per esempio per costruire un generatore termoelettronico
http://it.emcelettronica.com/diy-come-costruire-generatore-termoelettrico-12
http://it.emcelettronica.com/diy-come-costruire-generatore-termoelettrico-22
Esiste poi un doppio articolo per realizzare un frigorifero utilizzando le stesse celle, sistema attualmente utilizzate per i modelli commerciali alimentati a 12V
http://it.emcelettronica.com/costruiamo-frigorifero-con-le-celle-peltier-12
http://it.emcelettronica.com/costruiamo-frigorifero-con-le-celle-peltier-22
Per altri articoli sulle celle
http://it.emcelettronica.com/?s=peltier
grazie mille!! non mancherò di leggerli 🙂
non avrei pensato che la disposizione quasi casuale o meglio con un canale centrale vuoto o quasi avrebbe migliorato il profilo termico della scheda…….non si finisce mai di imparare…e molto interessante la segnalazione sui peltier ci passero presto a darci un occhiata
Complimenti per l’articolo. In effetti uno degli aspetti più importanti durante la progettazione elettronica è quello della dissipazione del calore, in quanto un componente che riscalda tende a ridurre drasticamente la vita utile. Purtroppo spesso ci si focalizza sulla sola posizione del componente sul PCB e non si passa ad una visione di sistema. Spesso i componenti che normalmente non riscaldano, si possono trovare a lavorare in ambienti critici a causa dei componenti vicino, con ovviamente una riduzione dell’affidabilità.