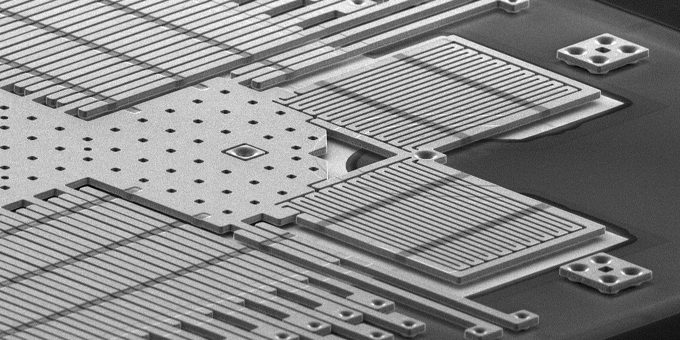
La proliferazione di sensori di qualità, combinata con la connettività affidabile e l’analisi dei dati, oltre a creare nuove efficienze industriali, rende i nodi intelligenti sempre più autonomi e mobili.
Introduzione
In un simile contesto, la precisione nel catturare il moto e tracciare la posizione del nodo sensore diventa fondamentale per il successo dell’applicazione. Le fattorie intelligenti sono in grado di sfruttare contemporaneamente veicoli terrestri a guida autonoma e droni per condurre più efficacemente le operazioni a terra, basandosi sui numerosi dati dei sensori geolocalizzati e sull’apprendimento analitico. La sala operatoria intelligente porta le tecniche di navigazione classiche sul tavolo chirurgico, con bracci robotici di precisione a guida remota che, grazie alla fusione dei dati provenienti dai sensori, garantiscono un movimento accurato in tutte le condizioni. In molti campi, dunque, i sensori basati sul movimento diventano un moltiplicatore di valore nelle applicazioni dinamiche.
La diffusione dei sensori inerziali di tipo consumer nei telefoni cellulari ha creato una certa sfiducia nel loro livello di accuratezza e, di conseguenza, fino a oggi non hanno avuto alcuna efficacia nel diffondere il concetto di Internet of Moving Things (IoMT). Tuttavia, le nuove generazioni di sensori industriali ad alte prestazioni sono in grado di supportare un’accuratezza di puntamento di frazioni di grado e una geolocalizzazione precisa. Grazie anche alle dimensioni e ai costi adeguati, esse rappresentano il futuro dell’IoMT.
Fattori di crescita del sensing intelligente nei sistemi industriali
I più importanti sviluppi nei macchinari e nei processi industriali sono volti all’ottenimento di vantaggi tangibili a livello di sistema, che di norma pongono sfide di progetto e implementazione, le quali a loro volta, portano a nuovi approcci risolutivi e nuovi modelli di business. A livello di sistema, i tre fattori chiave sono l’efficientamento delle risorse, l’accuratezza e il miglioramento della sicurezza. Le applicazioni che hanno puntato su questi miglioramenti sono largamente diffuse e spaziano tra aria/terra/mare, interni/esterni, breve/lungo termine e uomo/macchina. In ogni caso, come indicato in Tabella 1, fanno tutte affidamento su caratteristiche comuni, ovvero precisione, affidabilità, sicurezza, elaborazione e analisi intelligente dei dati.
In un’applicazione specifica i sensori di diverso tipo sono centrali nell’attività di progetto. La complessità dei sistemi rende necessario considerare con attenzione in fase di progetto qualità e robustezza del sensore, sotto diverse condizioni d’uso. Mentre alcune aziende hanno la possibilità di scegliere i sensori per convenienza (per esempio, sfruttando l’insieme dei sensori già esistenti in un telefono cellulare), altre definiranno il loro pacchetto di sensori partendo da zero, basando le loro scelte sulla precisione e combinandole con intelligenza per una copertura completa e affidabile degli stati previsti del sistema.
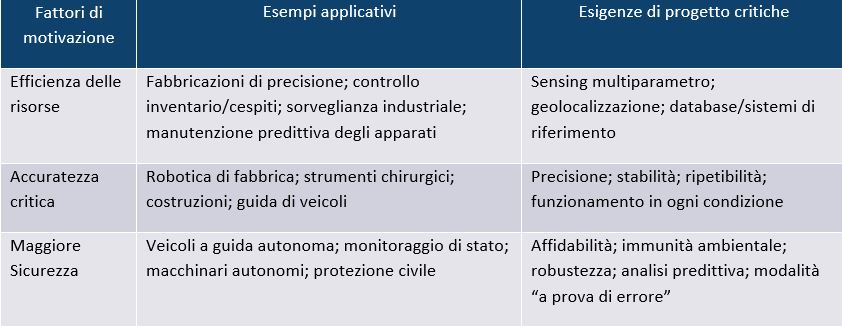
Tabella 1: i requisiti di sistema nelle applicazioni IoMT portano a esigenze di progetto impegnative
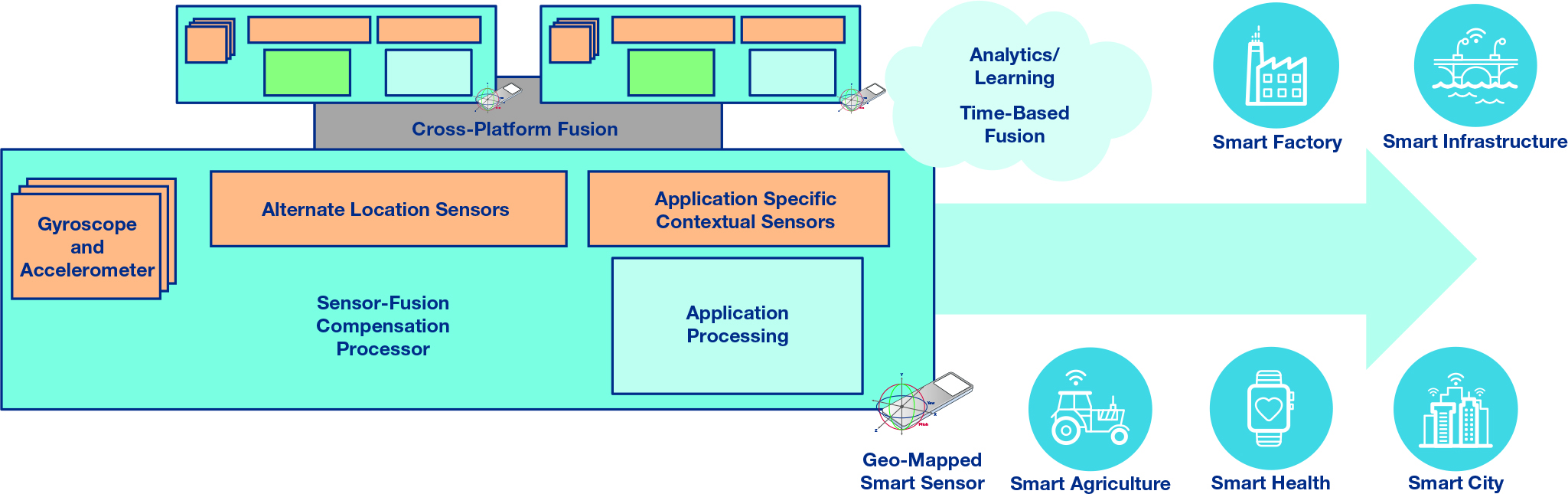
Figura 1: i requisiti industriali emergenti uniscono il sensing di movimento al contesto, su molteplici livelli di fusion
Smart Sensing
Nell’era dei sensori, questi sistemi intelligenti e accessibili stanno rivoluzionando anche i settori più tradizionali, trasformando l’agricoltura in agricoltura smart, le infrastrutture in infrastrutture smart e le città in smart city. Dato che per raccogliere informazioni contestuali rilevanti i sensori devono essere dispiegati sul campo, nella comunicazione e nella gestione del database insorgono nuove complessità, che richiedono una fusione sofisticata dei dati non solo tra i vari sensori, ma anche attraverso le diverse piattaforme e nel tempo (per esempio: l’analisi su cloud delle condizioni di un’infrastruttura nel tempo, il raccolto dell’anno precedente o le condizioni del traffico e i percorsi consigliati), come illustrato in Figura 1.
L’affidabilità delle informazioni che possono essere estratte dalle apparecchiature e dall’ambiente diventa il primo parametro di misura dell’utilità assoluta e della crescita di questi nuovi progetti. L’accuratezza, fondamentale anche per un funzionamento sicuro e affidabile, condiziona l’efficienza riflettendosi poi sugli aspetti economici. Anche se una semplice aggiunta di una caratteristica è possibile con i sensori più elementari, questo minimo valore aggiunto non è sufficiente quando si tratta di applicazioni IoMT, dove comandi come sì/no, su/giù o acceso/spento vengono sostituiti da una risoluzione infinitamente più alta e dalle implicazioni dell’aggiunta stessa sulla scelta del sensore.
Quando il movimento è importante
Nella maggior parte dei casi l’IoT è movimento. Anche quando non lo è, come nel caso di una telecamera fissa per la sicurezza industriale, resta essenziale la precisione del puntamento o, piuttosto, il riconoscimento di movimenti indesiderati (tampering). Un drone che cattura le riprese di un campo coltivato può dare risultati migliori e più veloci se è in grado di mantenere angoli di puntamento accurati anche in condizioni di volo difficili. Se i dati ricavati otticamente vengono poi geomappati con accuratezza è possibile anche effettuare raffronti storici di dati e variazioni. I veicoli smart, di terra, aria o mare, fanno sempre più affidamento su sistemi di guida GPS. Tuttavia, il GPS è esposto a rischi fisici o naturali (edifici, alberi, gallerie, etc.). Se scelti con cura, i sensori aggiuntivi possono affiancare il GPS per navigare con un’affidabilità maggiore durante le interruzioni di servizio. La Tabella 2 mostra un insieme di applicazioni IoMT in cui il fattore movimento è fondamentale.
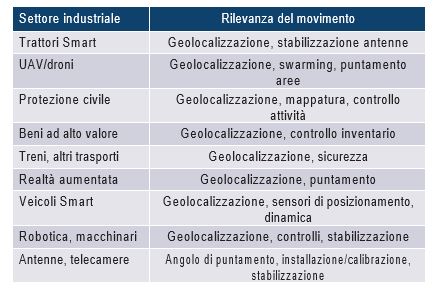
Tabella 2: il riconoscimento del movimento o della sua assenza sono fattori critici per il successo di molte applicazioni
L’importanza della conoscenza dello stato di un sistema aumenta se vengono dati opportunità e mezzi per catturare l’inerzia naturale di un apparato o di una persona, e se si possono fondere in modo appropriato con le informazioni contestualmente disponibili. Questo concetto è illustrato in Tabella 3.
Nodi IoMT affidabili e sicuri
La validità e il valore dei dati di un nodo IoMT dipendono principalmente dalla qualità dei sensori principali e dalla loro abilità di catturare fedelmente il contesto dell’applicazione. Il processo di fusione è quindi necessario per l’applicazione continua di correzioni/miglioramenti al sensore e per la dinamica di stato sensore-sensore ideale (ad esempio, quale sensore è il più affidabile in un determinato istante). L’elaborazione a livello di applicazione viene incorporata nella soluzione e ottimizzata secondo le specifiche ambientali, comprese le appropriate condizioni periferiche. Nonostante siano autonomi, in alcuni casi questi nodi lavorano in collaborazione, come nelle flotte di veicoli a guida autonoma, a terra o in aria.
In questi casi, vengono sviluppati canali di comunicazione sicuri, ponendo particolare attenzione all’affidabilità delle trasmissioni e alle identità univoche e protette, come illustrato in Figura 2.
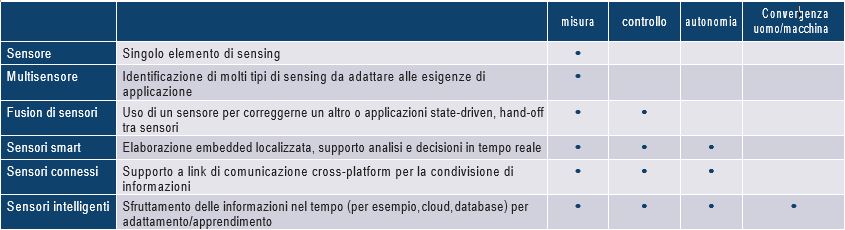
Tabella 4: partendo da una base di sensori di qualità, l’aumento di integrazione e intelligenza favorisce l’autonomia e la convergenza uomo-macchina
I sensori al centro dell’autonomia
Così come accade nel corpo umano, i nodi autonomi IoMT fanno affidamento su molteplici input sensoriali per raggiungere il livello di consapevolezza sufficiente ad agire in modo indipendente e ottimizzare le reazioni rispetto a eventi casuali e perfino caotici, con un deciso miglioramento nel tempo. Come si evince dalla Tabella 4, la transizione dalla misura elementare al controllo e all’autonomia richiede un crescente livello di complessità a livello di fusione di sensori, così come nell’intelligenza incorporata nel sistema. Dato che questi nodi raggiungono anche livelli elevati di interconnettività e apprendimento adattivo, essi tendono a far convergere uomo e macchina.
Ubicazione senza infrastruttura
Il GPS è disponibile ovunque, a meno che il segnale satellitare non venga bloccato o risulti assente. Se fruibili, le tecniche di localizzazione wireless possono essere molto precise. La lettura del campo magnetico è sempre disponibile in assenza di disturbi. L'inerzia invece è del tutto indipendente. Chiaramente, anche i sensori inerziali MEMS hanno le proprie lacune (deriva), ma sono gestibili e le nuove generazioni di Unità di Misura Inerziale (IMU) industriali forniscono una stabilità senza precedenti in package piccoli e convenienti.
I dispositivi inerziali MEMS sfruttano i processi produttivi standard per semiconduttori, packaging e approcci d’integrazione sofisticati per rilevare, misurare e interpretare direttamente i loro movimenti, tipicamente sotto forma di accelerazione lineare (g) o rotazione angolare (°/sec), come illustrato in Figura 3. Dato che tutte le applicazioni, tranne le più semplici, dispongono per definizione di molteplici gradi di libertà (essenzialmente, il movimento può avvenire su qualsiasi asse, e l’apparato è relativamente libero di muoversi), la misurazione dell’accelerazione e della velocità angolare deve essere effettuata per ciascuno degli assi x, y e z, a volte denominati “roll”, “pitch” e “yaw”. La loro combinazione viene indicata anche come unità di misura inerziale a sei gradi di libertà.
Anche se i vincoli di costo spingerebbero il progettista MEMS a utilizzare meno spazio possibile per ricavare su ogni asse (x, y, z) il maggior numero di rilevazioni (g, rate), per soddisfare il profilo di sensing industriale, più esigente, è necessaria una visione di progetto volutamente più equilibrata verso le prestazioni. Nella pratica ci sono strutture che tentano di misurare tutti i sei modi con un’unica massa MEMS. Prima ancora di esaminare la validità di un simile approccio per il sensing ad alte prestazioni, è importante comprendere che, mentre esistono movimenti la cui cattura viene effettivamente richiesta a un dispositivo MEMS, è ugualmente importante che lo stesso dispositivo sia in grado di ignorare o isolare altre forme di movimento che si traducono in errori di misura. Per esempio, mentre un giroscopio sta misurando una velocità angolare, dovrebbe anche essere in grado di ignorare l’accelerazione o gli effetti gravitazionali su quella specifica misura. Un dispositivo MEMS poco evoluto che cerca di misurare tutto con una struttura unica è, per sua stessa natura, del tutto suscettibile ad altre fonti di errore, e non è in grado di distinguere il movimento desiderato da quello indesiderato. In ultima analisi, tutto questo si traduce in rumore e in errori nella navigazione o nell’applicazione di puntamento.
Per far sì che l’IoMT mantenga le sue promesse per quanto concerne l’efficienza delle risorse, la sicurezza o l’accuratezza critica, è necessario disporre di un livello di precisione più elevato di quello ottenibile dalla massa di sensori meno evoluti universalmente presenti nei dispositivi mobili odierni. Progettare per le massime prestazioni significa sviluppare in modo indipendente ciascuna modalità e asse di sensing, ma con lo sguardo rivolto verso la fusione e l’integrazione. Infine, è importante notare che la progettazione rivolta alle prestazioni non deve avvenire a spese di quella rivolta alla convenienza.
Caratteristiche o prestazioni
Alcune applicazioni traggono vantaggi considerevoli dall’aggiunta di funzionalità (controllo gesto/orientamento di un dispositivo per il cambio di modalità) relativamente facili da estrarre con dispositivi MEMS di tipo semplice. Un dispositivo industriale o professionale può essere più adatto a misurare valori dell’ordine di qualche grado o di frazioni di grado, o può individuare una posizione secondo diversi ordini di grandezza, e nello stesso tempo funzionare in un ambiente a vibrazioni elevate. Le differenze di prestazioni tra sensori di fascia bassa e alta non sono poi così trascurabili, anzi, sono abbastanza vasta da meritare un’attenta considerazione durante la scelta del componente.
L’applicazione finale detta il livello di accuratezza necessario, e la qualità del sensore prescelto determina se questo è raggiungibile. La Tabella 5 mette a confronto due possibili soluzioni, illustrando l’importanza della scelta del sensore non soltanto sull’iter di progetto, ma sulla precisione dell’apparato. Un sensore di bassa precisione può in effetti essere adatto a un utilizzo limitato e a un’applicazione che tollera l’errore, in altre parole, se l’errore non è critico per la sicurezza o per l’incolumità, o se un’accuratezza relativamente modesta è sufficiente. Nonostante la maggior parte dei sensori di tipo consumer abbia una bassa rumorosità e si comporti adeguatamente in condizioni non critiche, essi non sono adatti a macchinari soggetti a movimenti dinamici e vibrazioni, che un’unità per la misura inerziale a basse prestazioni non è in grado di separare dalla misura della semplice accelerazione lineare o inclinazione desiderata.
Per raggiungere un’accuratezza superiore a un grado operando in un ambiente industriale, la selezione si concentra su sensori espressamente progettati per scartare la deriva di errori dovuti alle vibrazioni o all’influenza della temperatura. Un sensore ad alta precisione di questo genere è quindi in grado di supportare una gamma più ampia di stati di applicazione previsti per periodi più prolungati.
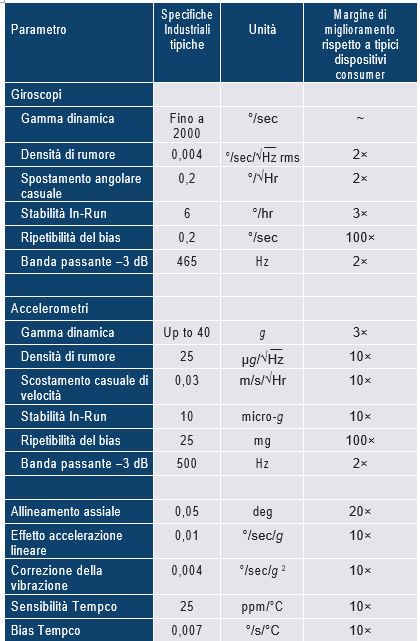
Tabella 6: i dispositivi MEMS industriali offrono la caratterizzazione estensiva di tutte le potenziali fonti di errore conosciute e raggiungono un miglioramento della precisione superiore a un ordine di grandezza rispetto ai tipi consumer
Di solito, i progettisti di strumentazione di precisione sono più interessati a lavorare con le unità di misura inerziale (IMU), che forniscono in uscita valori di g e rate calibrati, invece di angoli o distanze percorse, dato che queste informazioni a livello di sistema sono altamente specifiche rispetto all’applicazione. Questo riguarda l’attività principale del progettista di sistema, più che il progettista del sensore inerziale. Il problema consiste nel desumere, per esempio, l’accuratezza di puntamento di un sensore inerziale dalla tabella delle specifiche.
Nella Tabella 6, vengono illustrate le specifiche di un dispositivo industriale di livello medio, messe a confronto con un tipico sensore consumer reperibile in un telefono cellulare. Si noti che sono disponibili anche dispositivi industriali di livello più elevato, migliori di un ordine di grandezza rispetto a quelli indicati. La maggior parte dei dispositivi consumer di fascia bassa non fornisce specifiche per parametri quali effetto dell’accelerazione lineare, rettifica delle vibrazioni, spostamento angolare casuale e altri parametri che possono davvero rappresentare la prima fonte di errore nelle applicazioni industriali.
Questo esempio di sensore industriale è progettato per l’utilizzo in uno scenario che prevede movimenti relativamente o estremamente rapidi (2000°/sec, 40 g), dove l’uscita a banda larga di un sensore è altrettanto critica per permettere la migliore discriminazione del segnale. Durante il funzionamento si richiede una deriva minima dell’offset (stabilità in-run) per ridurre la dipendenza da un numero più elevato di sensori complementari, destinati a correggere le prestazioni. In alcuni casi la riduzione al minimo della deriva da accensione (ripetibilità) è critica in applicazioni che non possono disporre del tempo necessario per le correzioni eseguite da un sistema di filtraggio di back-end.
Per facilitare la distinzione e per correggere qualsiasi deriva correlata al fattore g, si utilizzano accelerometri a basso rumore unitamente a giroscopi.
I sensori giroscopici sono effettivamente progettati per l’eliminazione diretta dell’effetto di qualsiasi evento g (vibrazioni, urti, accelerazione, gravità) sull’offset del dispositivo, fornendo un vantaggio sostanziale in termini g-lineari. Attraverso la calibrazione sono stati corretti sia la deriva in temperatura sia l’allineamento. In assenza della correzione d’allineamento, un tipico dispositivo MEMS multi-asse, anche se integrato in un’unica struttura di silicio, può risultare disallineato al punto tale da essere la prima fonte di errore.
Se negli ultimi anni il rumore non è più un fattore di distinzione così determinante tra le classi di sensori, i parametri quali effetto g-lineare e disallineamento, che sono più costosi da correggere, sia attraverso un approccio di progetto, sia mediante la calibrazione specifica del componente, diventano fonti di rumore aggiunto in qualsiasi applicazione che vada oltre la determinazione del movimento semplice o relativamente statica.
Può la fusione tra sensori compensare la qualità modesta di un sensore?
Detto semplicemente, no. La fusione dei dati provenienti da sensori consiste in filtraggio e algoritmi che uniscono o gestiscono la combinazione di sensori, relativamente ad ambiente, dinamica del movimento e stato dell’applicazione. Può servire per rettifiche deterministiche come la compensazione in temperatura o per gestire il passaggio da un sensore all’altro, basandosi sulla conoscenza dello stato di sistema. Tuttavia, ciò non compensa le carenze specifiche del sensore.
Il compito più critico in un progetto a fusione di sensori è quello di sviluppare la conoscenza approfondita dello stato di applicazione, per gestire la parte restante dell’iter di progetto.
La scelta dei sensori appropriati per una data applicazione è seguita da un’analisi dettagliata per comprendere il loro peso (rilevanza) durante le diverse fasi dell’intera missione. Nell’esempio della navigazione stimata di un pedone, la soluzione è dettata principalmente dall’equipaggiamento disponibile (per esempio, i sensori installati in uno Smartphone), e non è progettata pensando alle prestazioni. Pertanto, si fa grande affidamento sul GPS assieme agli altri sensori disponibili, come quelli inerziali e magnetici a bordo, che offrono soltanto un contributo percentualmente modesto al compito di determinare informazioni utili sulla posizione. Questo sistema funziona ragionevolmente bene all’esterno, ma in un ambiente urbano o negli interni il GPS non è sempre disponibile, e la qualità dei sensori che rimangono è mediocre, lasciando uno scarto piuttosto ampio, o in altre parole, incertezza nella qualità dell’informazione sulla posizione. Anche se di solito per combinare i dati di questi sensori si utilizzano filtri e algoritmi avanzati, senza l’uso di sensori aggiuntivi o di qualità superiore il software risulta poco efficace per colmare realmente questi intervalli d’incertezza, il che in ultima analisi abbassa in modo significativo l’affidabilità della posizione riportata. Questo concetto è illustrato nella Figura 4.
In netto contrasto, lo scenario industriale della navigazione stimata è concepito a favore delle prestazioni. La definizione di sistema e la scelta dei componenti sono guidate da specifici requisiti di accuratezza. Sensori inerziali di qualità significativamente migliore possono assumere il ruolo primario, sfruttando attentamente gli altri sensori per ridurre l’intervallo d’incertezza. Concettualmente, gli algoritmi sono più focalizzati sulla pesatura ottimale, la gestione, e la correlazione incrociata tra sensori, assieme alla percezione delle dinamiche dell’ambiente a cui appartengono e del movimento real-time, estrapolando/stimando la posizione tra le letture affidabili del sensore.
L’accuratezza può essere in ogni caso aumentata attraverso sensori di qualità migliore e, anche se filtraggio e algoritmi rappresentano una parte critica della soluzione, da soli non compensano le carenze che derivano dall’uso di sensori di qualità limitata.
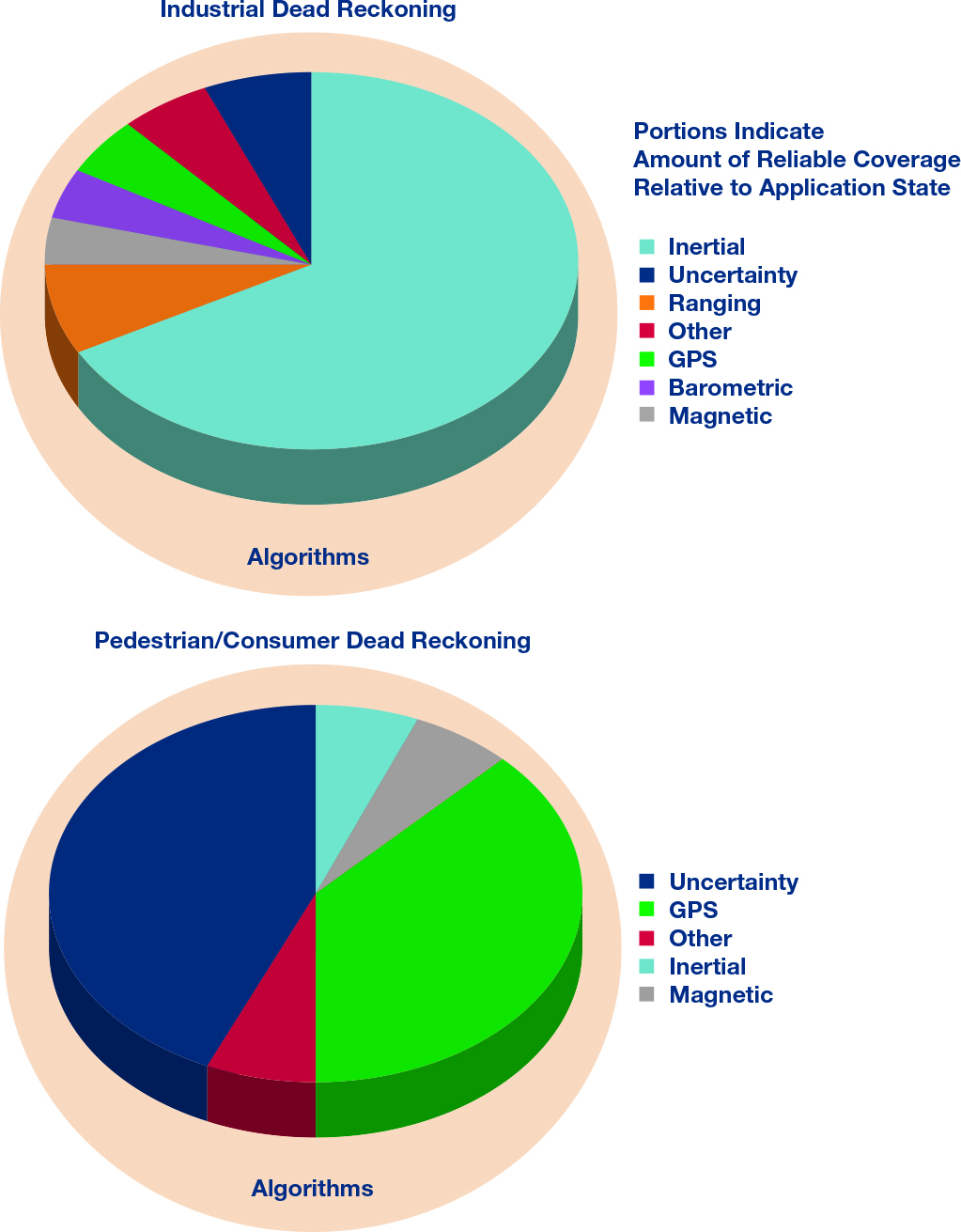
Figura 4: la precisione a livello di applicazione è determinata dalla qualità del sensore, non dalla sofisticazione della fusione di sensori
Le nuove classi di sensori industriali sono in grado di fornire prestazioni pressoché equivalenti a quelle utilizzate qualche tempo fa per la guida dei missili. Sfruttando le architetture di sensore concepite all’origine per l’utilizzo affidabile e preciso nelle applicazioni automotive e realizzate sulla base di processi scalabili ed economicamente percorribili, queste nuove generazioni di sensori industriali sono assolutamente uniche nei loro rapporti prestazioni/costo e prestazioni/dimensione, come visibile in Figura 5.
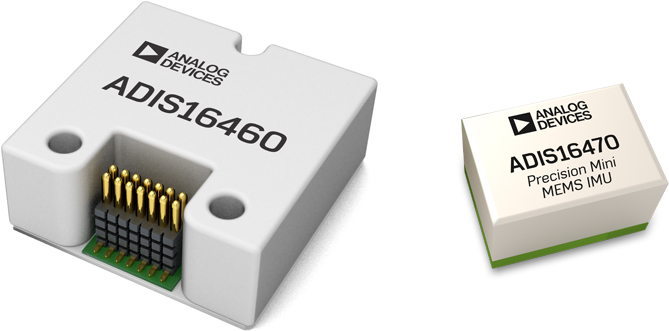
Figura 5: IMU industriali a sei gradi di libertà ADIS1647x e ADIS1646x, in grado di fornire letture di precisione anche in ambienti dinamici e complessi.
Il rilevamento di precisione del movimento non è più relegato ad applicazioni di nicchia, che non avevano altra scelta se non affrontare l’investimento in soluzioni di tracking dal costo proibitivo. Con la precisione di grado industriale disponibile in fattori di forma mini-IMU, oggi i progettisti IoT sono in grado di moltiplicare il valore fornito attraverso l’integrazione della rilevazione del movimento di qualità, combinata con il sensing contestuale embedded per abilitare l’IoMT.
A cura di Bob Scannell
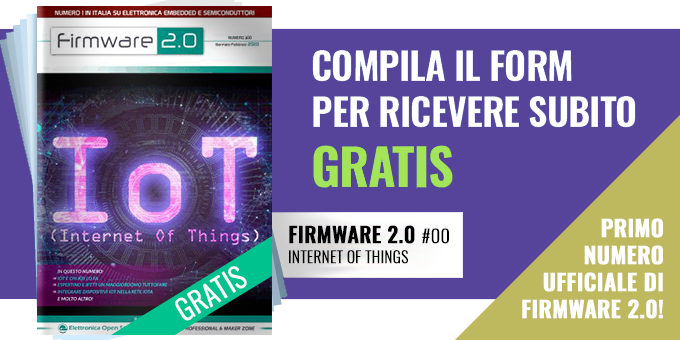