
Questo articolo esplora come l'AI viene utilizzata per il rilevamento dei difetti nei PCB. Descrive le tecniche, le fasi della produzione e le ricerche più recenti.
Introduzione
La produzione di circuiti stampati (PCB) è alla base di gran parte dell’elettronica moderna. Un PCB, acronimo di Printed Circuit Board, fornisce il supporto meccanico e le connessioni elettriche necessarie per assemblare dispositivi elettronici di ogni tipo, dai telefoni cellulari agli elettrodomestici, fino ai sistemi industriali e aerospaziali. I PCB definiscono il layout fisico delle connessioni tra i componenti elettronici e ne influenzano direttamente l'affidabilità: ogni piccolo difetto può compromettere il funzionamento o causare la riduzione delle prestazioni.
Ad oggi, il mercato globale dei PCB è dominato dall'Asia, con Cina, Taiwan, Corea del Sud e, a seguire, il Giappone come principali hub produttivi. La Cina, in particolare, è una filiera industriale completa a partire dalla produzione di materiali base come fogli di rame, fibra di vetro, resine e laminati rivestiti di rame, fino ai PCB finiti ed ai componenti elettronici. Attualmente, vi sono circa 2.500 produttori di PCB nella Cina continentale, concentrati principalmente nel Delta del Fiume delle Perle (conosciuto come Pearl River Delta), nel Delta del Fiume Azzurro (l'area cinese più sviluppata economicamente e con una forte densità di popolazione) e nella regione costiera del Bohai Rim, tutte aree caratterizzate da una logistica ottimale e da costi di produzione molto contenuti (i dati si trovano nell’ultimo rapporto sulle tendenze nel mercato dei circuiti stampati redatto da Mordor Intelligence, una società di ricerca e consulenza che si occupa di analisi di mercato e previsioni nei settori industriali).
Sempre secondo il rapporto, al di fuori dell'Asia, l’industria dei PCB è significativa anche in Europa e Nord America, dove produttori come AT&S (Austria) e Advanced Circuits (USA) hanno deciso di concentrarsi su applicazioni di fascia alta, come quelle aerospaziali o legate alla difesa ed al settore medicale. Allo stesso tempo, il mercato dei PCB è in crescita con una proiezione di valore di 80,33 miliardi di dollari nel 2024 e un tasso di crescita annuale del 4,87%, che lo porterà secondo le previsioni contenute nel rapporto, ad un valore di 96,57 miliardi di dollari entro il 2029. Tra i fattori trainanti ci sono la miniaturizzazione dei dispositivi che richiedono PCB compatti, leggeri e con una elevata conduttività termica, e la diversificazione applicativa dovuta ad una combinazione di fattori, tra cui le caratteristiche tecniche richieste dai dispositivi, le innovazioni nei materiali, e l'aumentare di funzionalità in mercati in crescita come l'IoT o il 5G.
I PCB tra design e sfide produttive
I PCB sono comunemente realizzati in fibra di vetro con strati conduttivi in rame, alternati a materiali isolanti. Possono variare da semplici schede a strato singolo, utilizzate per dispositivi di base, a strutture multistrato come quelle impiegate in schede grafiche e schede madri per hardware più complesso. Non esiste un design standard unico, mentre, le caratteristiche comuni includono tracce di rame, pad e piani per la connettività, rivestiti con maschere di saldatura e serigrafie per l'etichettatura dei componenti. La produzione dei PCB è articolata in più fasi, tra cui l'incisione, la laminazione e l'assemblaggio. Dopo la fabbricazione della struttura di base, i componenti elettronici vengono saldati e il prodotto finale viene sottoposto a test di qualità. Esistono tradizionalmente due tecniche di assemblaggio: la Surface Mount Technology (SMT), nata negli anni sessanta ma introdotta in modo significativo negli anni ottanta, che consiste nel posizionare i componenti direttamente sulla superficie del PCB e poi saldarli, e la tecnica a fori passanti o Through-Hole (THT) che prevede, appunto, l’inserimento dei componenti all'interno di fori che attraversano la scheda, con saldatura manuale o ad onda, ed è usata, prevalentemente, per applicazioni che richiedono una maggiore robustezza meccanica.
Durante il processo produttivo, come avviene per qualunque realizzazione, si possono verificare dei difetti, che compromettono le prestazioni del circuito o lo rendono inutilizzabile. I difetti possono essere di natura fisica come un graffio o una rottura, di natura elettrica, un cortocircuito ad esempio, oppure più strettamente di tipo strutturale come nel caso di componenti fuori posizione o addirittura mancanti. Rilevare i difetti nei PCB è essenziale soprattutto per prevenire guasti e ridurre i costi associati a scarti o in alcuni casi al richiamo del prodotto dal mercato. C'è da dire, però, che nel tempo, con l'aumento del numero di circuiti stampati e la diminuzione sempre più marcata delle loro stesse dimensioni, è diventato più difficile identificare efficacemente le anomalie o i difetti, ciò ha portato all’adozione di tecniche che superano i limiti della tradizionale ispezione manuale.
L'evoluzione dei processi di rilevamento dei difetti
L'ispezione manuale è stata a lungo il metodo principale per rilevare difetti nei PCB. Impiegare operatori esperti che osservano i circuiti stampati alla ricerca delle imperfezioni è ancora considerato un metodo basilare anche se poco scalabile sui grandi volumi, oltre che lento e soggetto a errori dovuti alla soggettività tipica di un operatore umano. A superare i limiti dell'ispezione manuale ci ha pensato l'ispezione ottica automatizzata, ovvero l'Automated Optical Inspection o AOI. Alla base dell’AOI, infatti, c'è un principio semplice: l’analisi visiva automatizzata che generalmente si concretizza attraverso l'uso di telecamere ad alta risoluzione accompagnate da illuminazione calibrata, per catturare immagini molto dettagliate del circuito stampato. Le immagini, nei sistemi moderni, vengono poi confrontate con un modello digitale di riferimento, e attraverso l'uso di algoritmi vengono individuate anomalie come componenti mancanti o disallineati oppure imperfezioni nelle saldature o altro ancora. Le versioni iniziali dell'ispezione ottica automatizzata si limitavano alla presenza di immagini bidimensionali mentre, oggi, i sistemi AOI 3D sono in grado di esaminare schede multistrato e rilevare problemi su componenti molto più complessi da analizzare puntando su fattori legati alla precisione e alla ripetitività per garantire accuratezza. Di fatto, sfruttano sensori per telecamere e proiettori per creare rappresentazioni tridimensionali e aumentare la precisione per poi ridurre significativamente i falsi positivi.
Sebbene l’AOI rappresenti una evoluzione nelle tecniche di identificazione dei difetti a partire dai metodi manuali, ha dei limiti, specialmente per quel che riguarda i componenti meno visibili dovuti ai diversi strati o a saldature nascoste, dove la sola visione ottica non basta. Per ovviare ad alcuni di questi limiti si è diffusa l’ispezione a raggi X che arriva ad analizzare l’interno dei PCB e delle saldature, individuando difetti come vuoti o microfratture nei giunti. L’ispezione a raggi X, utile per i formati particolari come i contenitori di BGA (Ball Grid Array) che più di tutti, per forma e per come sono costituiti, hanno componenti meno visibili, è molto costosa. Inoltre, non è semplice da implementare perché richiede competenze specifiche per interpretare e identificare, ovvero per individuare in modo definitivo, il difetto. Altra modalità e altro metodo non di natura visiva, è il test elettrico che si basa sull'uso di sonde per verificare la continuità dei circuiti e identificare cortocircuiti. Viene, però, generalmente combinato con altre tecniche e, come si può intuire, non serve per eliminare difetti materiali o di tipo meccanico.
ATTENZIONE: quello che hai appena letto è solo un estratto, l'Articolo Tecnico completo è composto da ben 2539 parole ed è riservato agli ABBONATI. Con l'Abbonamento avrai anche accesso a tutti gli altri Articoli Tecnici che potrai leggere in formato PDF per un anno. ABBONATI ORA, è semplice e sicuro.
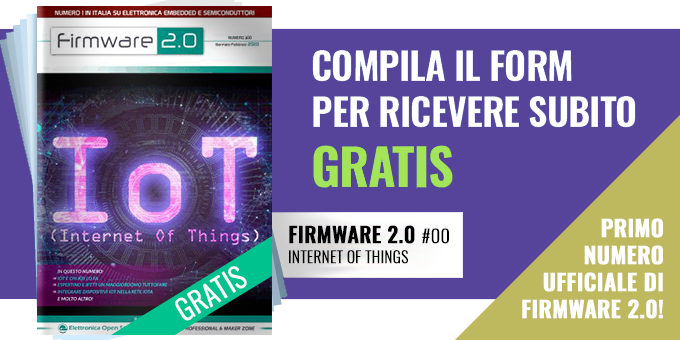