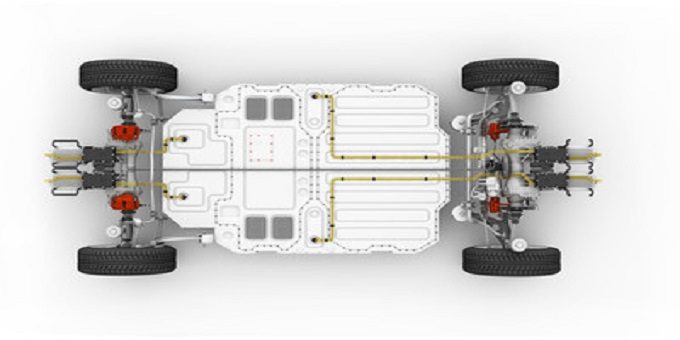
Ricordate la battuta nel film Crocodile Dundee: "Quello è un coltello? Questo è un coltello! ". Nel mondo dei veicoli elettrici l'espressione si traduce come "Quella è una batteria? Questa è una batteria! ”. I veicoli elettrici (EV) sono alimentati da enormi banchi di batterie, costruiti con lunghe file di batterie in serie (Figura 1). Questi banchi di batterie, tipicamente costituiti da celle agli ioni di litio (Li +), possono raggiungere tensioni di funzionamento superiori agli 800 V. Tuttavia, i materiali delle batterie aventi questa composizione chimica possono essere danneggiati se vengono sovraccaricati. Ogni tensione di cella deve essere monitorata e, se necessario, devono essere applicati metodi di controllo adeguati per evitare sovratensioni. Un'eccessiva corrente di dispersione delle celle, sovratensione, sotto tensione e temperature estreme possono portare a prestazioni più deboli o persino a guasti catastrofici.
La tipica batteria EV rappresentata in Figura 2 è costituita da 6720 celle Li + gestite da otto moduli di controllo. Ciascuna cella ha una capacità di 3.54 Ah, raggiungendo fino a un totale di accumulo di energia nominale della batteria di 100 kWh (3.54 Ah x 4.2 V x 6720 celle). La serie di 96 righe, ciascuna composta da 70 celle in parallelo, raggiunge una tensione della batteria di 403.2 V (96 righe x 4.2 V), con una capacità di 248 Ah (100 kWh/403.2 V o 3.54 Ah x 70 colonne).
Ciò consente ad un EV di percorrere 300 miglia a una velocità di 50 miglia all'ora per 6 ore prima che la batteria si esaurisca. Il motore EV assorbirà una corrente media di 41A (248Ah/6h). Nella configurazione a catena di Figura 2, tutti i moduli di controllo comunicano in serie con un microprocessore centrale tramite IC1. È richiesto l'isolamento tra il microprocessore ed il primo modulo e da un modulo al successivo. Il collegamento dati deve funzionare in modo affidabile in ambienti rumorosi e ad alta potenza della batteria, dove sono presenti sia il rumore dell'alta tensione dV/dt che l'iniezione di corrente in modalità comune (indotta da campi elettromagnetici).
Sfortunatamente, quando si tratta di pacchi batteria, molte cose possono andare per il verso sbagliato. Prestazioni indebolite o persino guasti catastrofici possono essere innescati da un'eccessiva dispersione di corrente, alta o bassa tensione e temperatura estrema delle celle. La manifestazione di questi guasti varia con la configurazione della cella della batteria. In uno stack di celle in serie, le variazioni di tensione sono individuate più facilmente, mentre, in configurazioni parallele, la corrente di dispersione viene amplificata. In una configurazione mista in serie ed in parallelo, come quella della Figura 2, le deviazioni nella corrente di dispersione vengono misurate più facilmente mentre le deviazioni di tensione indotte da una singola cella difettosa vengono attenuate e richiedono misurazioni con un livello di precisione più elevato.
A questo punto non si possono davvero sovraccaricare le batterie Li + e le batterie ai polimeri di litio senza danneggiare i loro materiali attivi. In una fila di celle in serie, è necessario monitorare lo state-of-charge (SOC) di ciascuna tensione di cella. Se necessario, è opportuno applicare metodi di controllo adeguati per evitare sovratensioni dovute a sovraccarico. Le celle in parallelo tendono ad auto-bilanciarsi poiché la connessione parallela mantiene tutte le celle alla stessa tensione per impedire la tensione di fuga di una singola cella. Di conseguenza, in una matrice di celle come in Figura 2, il monitoraggio procede da una fila di celle, anziché da una singola cella. Ciascun modulo mostrato contiene tutta l'elettronica necessaria per eseguire il bilanciamento mediante matrici di interruttori e con resistori collegati attraverso i nodi delle celle.
L'accuratezza della misurazione della tensione della cella è importante per motivi di sicurezza e per massimizzare la capacità della batteria. Ogni millivolt di inesattezze si traduce alla fine in un ridotto utilizzo della batteria. La precisione è uno dei parametri che grava pesantemente sullo state-of-health (SoH) e sul SOC della batteria.
L'Automotive Safety Integrity Level (ASIL) è uno schema di classificazione dei rischi definito dallo standard ISO 26262. Esistono quattro livelli di rischio identificati dagli standard da ASIL A ad ASIL D, con quest'ultimo corrispondente al livello di rischio più basso. Un IC conforme ASIL è dotato della diagnostica necessaria per rilevare condizioni di guasto specifiche.
Uno smart sensor automotive di acquisizione dati per IC risolve problemi come la sicurezza delle celle, la diagnostica e il bilanciamento. Il MAX17843 è un'interfaccia di monitoraggio della batteria ad alta tensione programmabile con ampie funzionalità per la sicurezza. Il front-end analogico (AFE) combina un sistema di acquisizione dei dati di misurazione della tensione a 12 canali con un input switch-bank ad alta tensione. Ciascuno degli otto moduli in Figura 2 è alimentato da un singolo IC. Due ingressi analogici ausiliari possono essere usati per misurare componenti di termistori esterni. Un termistore a coefficiente di temperatura negativo (NTC) può essere configurato con gli ingressi analogici AUXIN per monitorare accuratamente la temperatura del modulo o della cella della batteria. Un rilevatore di sovraccarico termico disabilita il regolatore lineare di bordo per proteggere l'IC. È inoltre disponibile una misurazione della temperatura della matrice.
Per saperne di più, dai un'occhiata a MAX17843EVKIT, il kit di valutazione che ti consente di valutare questa parte per il tuo prossimo progetto automobilistico. Questo blog post è stato adattato da una soluzione progettuale, “Monitor Your Electric Vehicle’s Battery with a Smart Sensor.”
Articolo pubblicato da Reno Rossetti PhD., EE, Maxim Integrated - versione originale in inglese sul sito "Maxim Integrated".
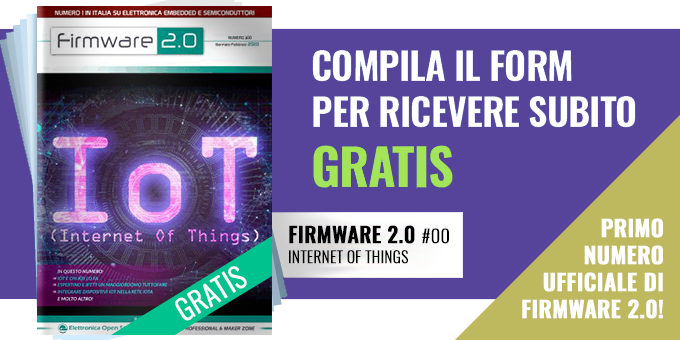
Interessante articolo, effettivamente ero interessante a sapere come era possibile gestire tutta la potenza fornita dalle batterie necessaria per il funzionamento del veicolo.
Sicuramente questi componenti saranno messi a dura prova specialmente in caso di incidente. Anche se credo che in questo caso intervengano altri dispositivi. Questo per il fatto, già evidenziato, che in caso di incidente le batterie possano incendiarsi ed essendo un incendio di una sostanza metallica è difficile da controllare.
Concordo, la vera sfida del futuro non sono le performance ma le performance in relazione al livello di sicurezza.
Bell’articolo. Un po’ alla volta andremo ad approfondire quali sono le informazioni necessarie e come sono fatti i singoli sistemi che compongono un auto elettrica, Sarebbe utile una selezione di produttori di batterie, oltre che di circuiti di monitoraggio di carica/scarica.