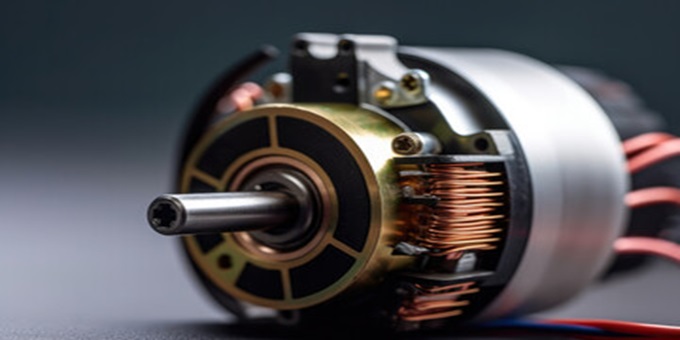
Direttamente dalla rivista cartacea Firmware, pubblichiamo una nuova serie di articoli per la Rubrica Firmware Reload. Molte applicazioni dei motori elettrici richiedono doti di robustezza, affidabilità e flessibilità nel controllo della velocità. I motori Brushless sono sempre più diffusi proprio perché sono in grado di rispondere a queste esigenze, grazie all’impiego di efficienti circuiti di controllo generalmente basati sull’impiego di sensori a effetto Hall.
Come è logico immaginare, maggiore è il numero di poli, maggiore è il numero di commutazioni che sono necessarie per avere un giro completo del rotore; la velocità del rotore, a parità di altre condizioni, è quindi inversamente proporzionale al numero di poli. Il rotore presenta tipicamente un numero di poli compreso tra due e otto che si alternano N-S. Il principio di funzionamento può essere visto anche in maniera più elementare: assunto che il magnete del rotore produce un flusso magnetico, se si alimenta la fase F1 del motore, si produce una coppia che tende ad allineare i due campi trascinando in rotazione il rotore fino ad annullare la coppia stessa, da cui la necessità di alimentare le fasi secondo una opportuna sequenza, se si vuole mantenere costante la rotazione. In un motore brushless a tre fasi, ciascuna fase è interessata a valle dell’inverter da un funzionamento in regime alternativo (il che non significa necessariamente sinusoidale). La logica di commutazione che pilota l’inverter può essere efficacemente implementata attraverso un microcontrollore. Controllando la frequenza di commutazione dell’inverter e le correnti che circolano in esso, è possibile controllare la velocità e la coppia del motore.
Dal punto di vista degli avvolgimenti si tratta quindi di motori generalmente trifasi anche se esistono motori brushless, specie di piccola potenza, a due soli avvolgimenti di statore (Figura 2). Dal punto di vista del funzionamento e più precisamente dell’interazione elettromagnetica tra avvolgimenti di statore e di rotore, se si analizza il funzionamento del motore visto a valle dell’inverter, si capisce che si tratta di un motore AC sincrono con rotore a magneti permanenti. Il principio di funzionamento del motore brushless è in sostanza lo stesso di un motore in c.c. a magneti permanenti in cui rotore e statore siano stati scambiati: i magneti sono sul rotore e gli avvolgimenti sullo statore mentre la funzione di commutazione non è più realizzata dal collettore ma dall’inverter e dall’elettronica di controllo. Per commutare l’alimentazione delle fasi nel modo opportuno occorre conoscere istante per istante la posizione dei poli del rotore (informazione che nel motore in c.c. è intrinseca nel sistema collettore-spazzole) da cui l’impiego di sensori magnetici a effetto Hall (o, più raramente, di encoder ottici). A voler essere più precisi, esistono due tipi di motore brushless: brushless DC (o trapezoidali) e brushless AC (o sinusoidali). Il brushless trapezoidale presenta un rotore con magnetizzazione tale che, una volta posto in rotazione, produce sugli avvolgimenti statorici una f.e.m. indotta con profilo trapezoidale. Il motore brushless AC è in invece un’evoluzione di quello DC. Lo statore viene alimentato da una terna di correnti sinusoidali sfasate tra loro di 120° elettrici; la f.c.e.m. ha anch’essa andamento sinusoidale, cosa che si ottiene magnetizzando opportunamente il rotore. A parte questo dettaglio, i due motori sono del tutto simili. Pilotando opportunamente gli avvolgimenti statorici si ha quindi lo sviluppo di una coppia proporzionale alla forza controelettromotrice e alle correnti di statore. E’ interessante sottolineare che le tre fasi di statore sono alimentate con tre correnti alternate, per cui ciascun avvolgimento genera un campo magnetico alternato. Se le correnti di eccitazione sono opportunamente sfasate, i tre campi si sommano, dando origine a un campo magnetico che risulta costante nel modulo, ma rotante con velocità angolare proporzionale alla frequenza delle tre correnti alternate. Nel rispetto del principio generale di funzionamento di un motore elettrico, i campi magnetici di statore e di rotore, interagendo tra loro, danno origine a forze di attrazione tra poli di segno opposto che tendendo ad allineare i due campi, mettendo in rotazione il rotore. La coppia è massima quando i due campi magnetici sono ortogonali fra loro e nulla quando sono allineati ed è per questo, se si vuole mantenere in rotazione il rotore, che risulta necessario mantenere sempre un opportuno sfasamento spaziale tra campo magnetico di statore e campo magnetico di rotore.
Da ciò, nasce la necessità di commutare opportunamente le correnti negli avvolgimenti di statore, in funzione della posizione del rotore, attraverso l’impiego di un controllo elettronico a commutazione costituito da un inverter e un controller che contemporaneamente abbia informazione sulla posizione del rotore (tramite un encoder o sensori ad effetto Hall). In ogni caso, che il motore sia pilotato attraverso tensioni rettangolari, trapezoidali o sinusoidali, purché alternate, sfasate tra loro di 120 ° e fasate opportunamente con la posizione del rotore, l’angolo tra il flusso magnetico di rotore e quello di statore viene mantenuto sempre vicino a 90° in modo da ottenere la coppia massima. L’inverter, pilotato opportunamente, trasforma la tensione continua in tre tensioni alternate tali da generare il campo rotante di statore. La possibilità di controllare frequenza e ampiezza (o valor medio) di queste tensioni si tramuta nella possibilità di controllare l’intensità e la velocità di rotazione del campo magnetico rotante e quindi la coppia e la velocità del rotore con il cui campo magnetico interagisce. Il motore visto dall’esterno rimane alimentato in corrente continua ed è per questo spesso indicato anche come motore in continua senza spazzole. In ogni caso, il controllo della velocità non può essere ottenuto attraverso un semplice potenziometro (energeticamente inefficiente ma estremamente poco costoso) come nei motori brushed DC, ma necessita del controllo elettronico che attua la necessaria commutazione delle fasi. I motori brushless (Brushless DC electric motor o BLDC motor o BL motor) sono per questo anche noti come motori a commutazione elettronica (Electronically Commutated Motor, ECM, EC motor). In un certo senso, si tratta anche di una macchina sincrona, dal momento che i campi di rotore e di statore sono sempre mantenuti sincroni e sfasati tra loro per creare la coppia motrice.
APPLICAZIONI DEI MOTORI BRUSHLESS
L’ingombro limitato rispetto alla potenza sviluppabile e la caratteristica di coppia sono vantaggiosi in tutte le applicazioni in cui è necessaria compattezza fisica, mentre l’impossibilità di generare scintille è vantaggiosa per le applicazioni in atmosfere sature di composti chimici volatili e potenzialmente infiammabili. L’efficienza energetica e il controllo elettronico completano il quadro delle caratteristiche maggiormente apprezzate dei motori brushless. Le applicazioni sono di conseguenza molteplici e spaziano dai tradizionali meccanismi di rotazione di floppy disk, lettori e masterizzatori CD, DVD e hard disk a quelli utilizzati nell’automodellismo e nell’aeromodellismo (Figura 1).
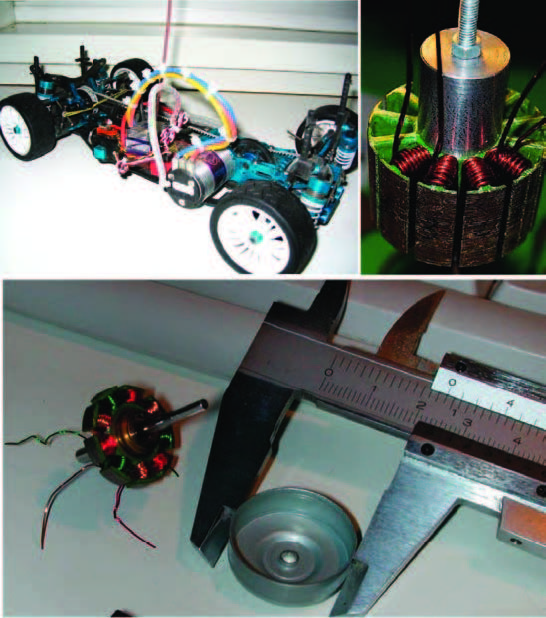
Figura 1: La caratteristica di poter essere realizzati anche di piccole potenze e l’accurato controllo della velocità rendono i motori Brushless molto utilizzati nell’automodellismo e aeromodellismo
L’efficienza energetica, la compattezza, la controllabilità e l’affidabilità sono caratteristiche che ne hanno permesso l’impiego anche nei sistemi di condizionamento e refrigerazione e nei sistemi di dissipazione controllata che impiegano ventole di dissipazione (molto usate in campo informatico - Figura 2).
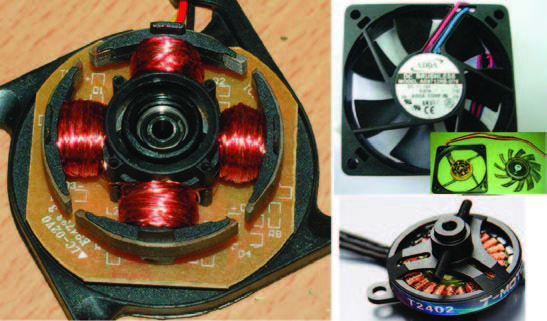
Figura 2: Particolari di alcuni Brushless utilizzati nelle ventole di dissipazione per PC. A sinistra è mostrato un brushless a due fasi e quattro poli in cui è stata rimossa la parte rotante al fine di rendere visibili gli avvolgimenti di statore. Questi e le espansioni polari sono meccanicamente solidali con il PCB e l’elettronica
I motori BLDC hanno via via sostituito i motori DC brushed anche in molti ambiti industriali, specie nei settori dell’automazione, in cui è richiesto il controllo del movimento attraverso l’impiego di servomotori come quelli che equipaggiano robot e macchine CNC. Le buone caratteristiche coppia-velocità, l’elevata efficienza e i bassi costi di manutenzione sono risultate, anche in questo caso, importanti per la loro affermazione. Per comprendere quanto possa essere utile un motore di questo tipo in questo ambito, è sufficiente pensare alla movimentazione di un pezzo mediante braccio motorizzato (pick and place). Il ciclo di lavoro è quello tipicamente ripetitivo di una catena di montaggio: il braccio individua il pezzo, lo cattura, lo trasporta, lo rilascia nella posizione destinazione e si riposiziona opportunamente nel punto in cui è disponibile un nuovo pezzo da movimentare. Nei momenti di presa e di rilascio del pezzo, si manifesta una notevole variazione di coppia resistente che è all’origine di notevoli forze controelettromotrici (f.c.e.m), sovratensioni e sovracorrenti. Una situazione operativa del genere sarebbe causa di scintillii, nel caso in cui venissero utilizzati motori DC brushed.
Questo è uno dei motivi per cui i motori brushless vengono oggi utilizzati in molte applicazioni industriali che prevedono la movimentazione automatica. I vantaggi dei motori brushless sono più in generale evidenti nei servo-azionamenti, poiché in questo ambito sono necessari controllo di velocità e posizionamento, inversione rapida del senso di rotazione, precisione nel posizionamento, regolarità di marcia a basse velocità, rapidissime accelerazioni o decelerazioni, robustezza e coppie elevate, di spunto e a regime. Non è tutto: il motore brushless sta diventando la soluzione preferita in tutte le nuove apparecchiature ad elevato risparmio energetico, cioè di fatto il motore preferito negli elettrodomestici. Frigoriferi, ventilatori, condizionatori (tra le prime macchine utilizzate in ambito domestico ad equipaggiarsi di questo tipo di motore), lavatrici, che tradizionalmente impiegavano motori a induzione in AC, traggono oggi vantaggio dalla disponibilità di questi motori. Maggiore efficienza energetica (e quindi contenimento dei consumi), coppia costante su un ampio intervallo di velocità, minore ingombro e minore rumorosità, controllabilità in diverse modalità operative, minore rumore elettrico rispetto ai motori DC brushed, minore necessità di manutenzione e il fatto di essere ormai economicamente competitivi sul mercato li rendono più che preferibili anche in questo ambito. L’impiego del cosiddetto controllo a orientamento di campo (FOC-Field Oriented Control) o controllo vettoriale, una tecnica di controllo elettronico che offre efficienza nettamente superiore rispetto alle altre tecniche di controllo, che riduce le vibrazioni, aumenta la precisione del movimento e che può essere realizzato in modalità “sensorless” (di cui parleremo successivamente) rende ancora più performante il loro impiego. Ne consegue che oggi siamo circondati da un’infinità di apparecchiature che integrano i motori brushless.
Agli ambiti già citati vanno aggiunti il settore dei veicoli elettrici come biciclette elettriche (con potenze generalmente di poche centinaia di watt) e auto elettriche (con potenze anche di qualche decina di chilowatt) e quello degli elettroutensili, campo applicativo in cui è richiesto il controllo della velocità, che è simile per molti aspetti a quello degli elettrodomestici (Figura 3 e Figura 4). In campo automobilistico la diffusione dei motori BLDC trova in realtà oggi terreno ancora più fertile. Un’automobile è infatti oggi dotata di impianti che contemplano diversi tipi di motori (per l’azionamento delle pompe dell’olio, dell’acqua e della benzina, delle ventole o degli impianti di climatizzazione, per l’azionamento degli alzacristalli elettrici, dei tergicristalli, per la regolazione della posizione degli specchietti retrovisori o dei sedili). In conclusione, i motori brushless vengono utilizzati oggi in molte applicazioni tradizionalmente occupate dai motori DC brushed o AC a induzione. Il loro impiego è inoltre vantaggioso in applicazioni che prevedono l’impiego di batterie e che traggono quindi vantaggio dalla loro elevata efficienza. E’ il tipico caso degli elettroutensili portatili (Figura 4).
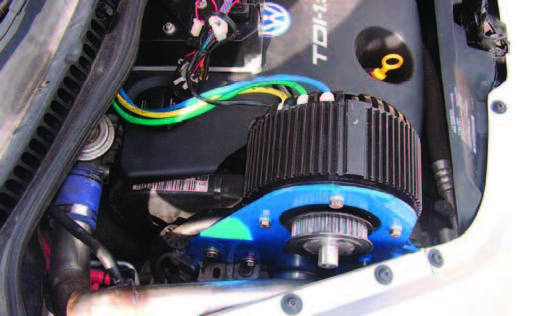
Figura 3: La caratteristica dei motori Brushless di poter essere realizzati anche di potenze medio-alte e l’accurato controllo della velocità, li rendono utilizzabili nella realizzazione di veicoli come biciclette e auto elettriche
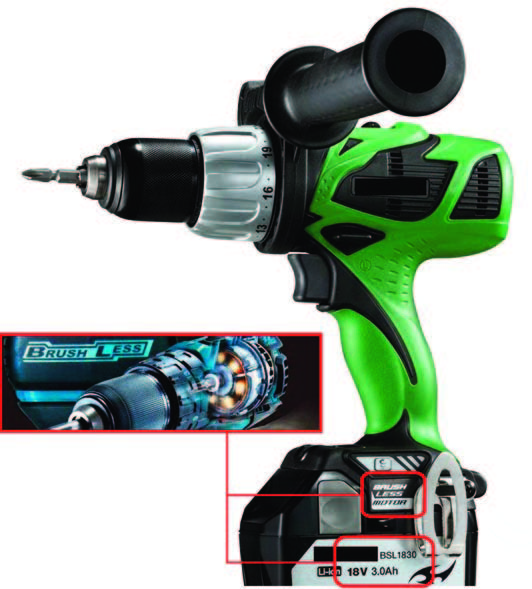
Figura 4: Motori Brushless di potenze comprese tra poche decine e qualche centinaia di watt sono utilizzati per la realizzazione degli elettroutensili portatili che necessitano di regolazione della velocità. Il loro impiego è ancor più vantaggioso nella realizzazione di elettroutensili a batterie grazie all’elevata efficienza
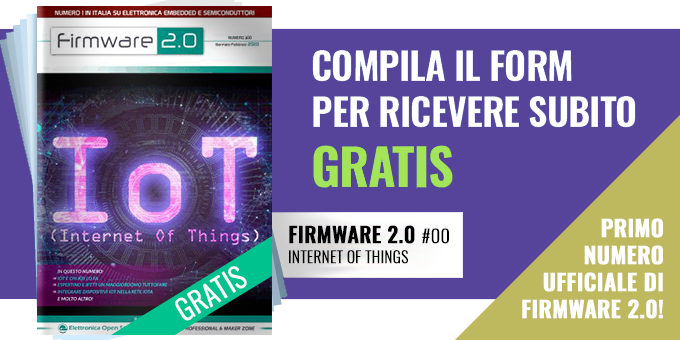