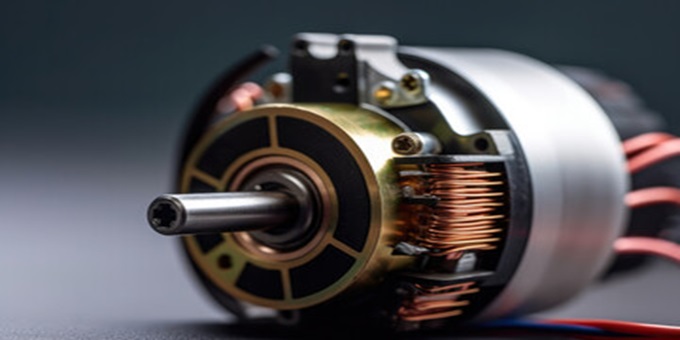
Direttamente dalla rivista cartacea Firmware, pubblichiamo una nuova serie di articoli per la Rubrica Firmware Reload. Molte applicazioni dei motori elettrici richiedono doti di robustezza, affidabilità e flessibilità nel controllo della velocità. I motori Brushless sono sempre più diffusi proprio perché sono in grado di rispondere a queste esigenze, grazie all’impiego di efficienti circuiti di controllo generalmente basati sull’impiego di sensori a effetto Hall.
ELETTRONICA DI CONTROLLO
Per il controllo della rotazione è necessario un sistema di rilevamento della posizione del rotore rispetto allo statore. A tale scopo, è possibile utilizzare sensori ad effetto Hall oppure encoder ottici. Scopo del controllo è prima di tutto quello di ottenere, attraverso il controllo delle correnti statoriche, una coppia costante, indipendente dalla posizione angolare del rotore. In pratica, la commutazione elettronica di un motore brushless avviene eccitando in sequenza gli avvolgimenti di statore in funzione della posizione del rotore. Attraverso un’opportuna manipolazione delle forme d’onda di tensione e di corrente applicate agli avvolgimenti di statore, si ottiene il controllo della velocità e della coppia. Tale elettronica si integra con la funzione di encoder normalmente svolta dai sensori a effetto Hall, utili a determinare istante per istante la posizione del rotore. Dall’acquisizione di questa informazione l’elettronica di controllo deduce l’orientamento da imprimere al campo magnetico che deve essere generato dallo statore e pilota di conseguenza i tre avvolgimenti, in modo da trascinare il rotore nella direzione corretta. Modulando la corrente negli avvolgimenti è possibile accelerare o rallentare il motore, che è contemporaneamente soggetto alla coppia resistente dovuta al carico. Orientando il campo magnetico statorico in modo opportuno è inoltre possibile frenare il rotore stesso. In Figura 1 è riportato uno schema logico-funzionale del controllo appena descritto. Con riferimento ad un diagramma coppia-velocità (Figura 2), la regolazione della velocità può avvenire, a seconda del sistema di controllo, a 1, 2 o 4 quadranti.
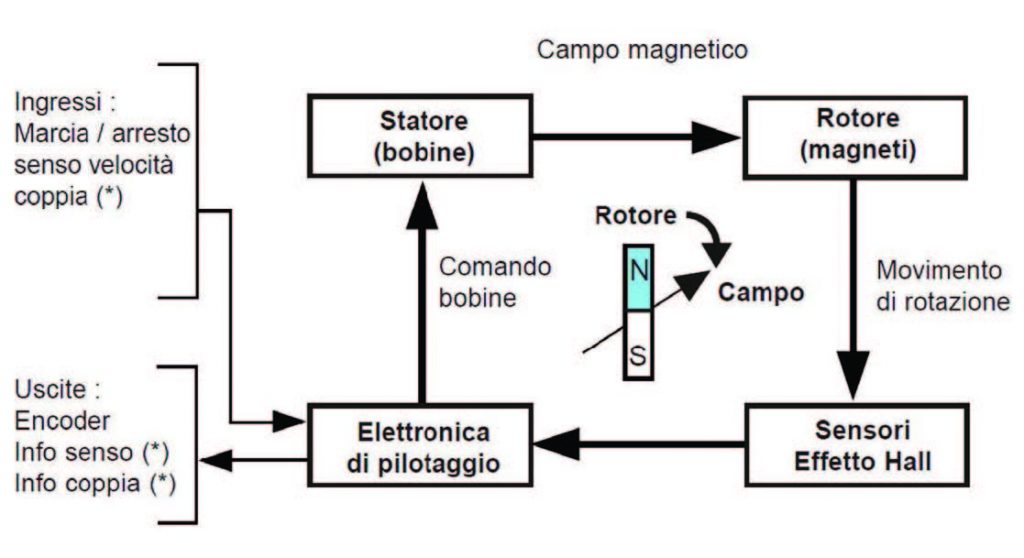
Figura 1: Schema logico-funzionale del controllo di velocità di un motore brushless
Una velocità positiva rappresenta una rotazione in senso orario, una velocità negativa in senso antiorario, una coppia positiva un funzionamento motore, una coppia negativa un funzionamento freno. Una regolazione a 1 quadrante consente il funzionamento del motore in un solo senso di rotazione, senza possibilità di frenatura. In caso di eccessiva velocità, il controller interrompe la corrente lasciando che il rotore venga frenato dalla coppia resistente. In una regolazione a 2 quadranti il funzionamento è analogo nei due sensi di rotazione. Una regolazione a 4 quadranti è invece analoga a quella a due quadranti ma in caso di eccessiva velocità, il motore partecipa esso stesso alla frenatura, assorbendo energia dal sistema meccanico. A seconda di come avviene tale assorbimento, si ha la “frenatura con rigetto d’energia“ che converte l’energia in corrente elettrica rigettata verso l’alimentazione (e che, ad eccezione dei sistemi a batteria, comportano ritorni di corrente dannosi) e “frenatura con dissipazione di energia” che converte l’energia cinetica del sistema in calore. Il controllo della velocità può ottenersi variando, fissata la forma d’onda, il valore delle correnti di eccitazione e quindi delle tensioni di eccitazione delle fasi oppure il loro valor medio. Per agire sul valor medio è allora possibile impiegare la modulazione a larghezza d’impulso (Pulse Width Modulation) dell’eccitazione. La coppia e la velocità del motore dipendono in questo caso dal rapporto Ton/Toff dei transistor componenti l’inverter. La coppia dipende infatti da parametri fissi del motore, come le dimensioni del rotore e il numero di avvolgimenti di statore, ma anche dalla corrente media che circola nello statore. Per ottimizzare la coppia, il campo di statore deve essere in quadratura con il campo di rotore. Il controller del motore deve quindi generare opportunamente le forme d’onda di statore in funzione della posizione del rotore. Un controllo preciso diviene quindi più difficoltoso a velocità elevate, dal momento che più aumenta la velocità e più un dato ritardo nella forma d’onda che pilota un avvolgimento diviene inaccettabile. In pratica, un ritardo tende a ridurre la coppia sviluppata, a sviluppare forze che sollecitano inutilmente i cuscinetti del rotore e ad aumentare allo stesso tempo il rumore acustico.
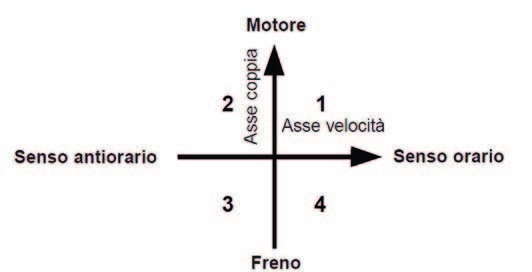
Figura 2: Quadranti di funzionamento di un motore elettrico. Una velocità positiva rappresenta una rotazione in senso orario, una velocità negativa in senso antiorario, una coppia positiva un funzionamento motore, una coppia negativa un funzionamento freno
CONTROLLO DELLA POSIZIONE
Il modo più comune di rilevare la posizione del rotore è, come già accennato, quello di utilizzare dei sensori Hall. Funzionalmente, possono essere visti come un set di switch ad attivazione magnetica. Ciascuno switch si apre o chiude quando il campo magnetico supera o va al di sotto di determinati valori di soglia. Un motore BLDC a tre fasi impiega tre sensori Hall fissati sulla parte statica del motore (statore) su una apposita scheda elettronica, alloggiata nella zona opposta a quella su cui è resa disponibile la coppia motrice. A seconda delle scelte costruttive, possono fare da trigger magneti allineati con il campo di rotore oppure gli stessi magneti di rotore. Ogniqualvolta un polo del rotore passa in prossimità dei sensori Hall, questi forniscono un segnale alto o basso. I segnali digitali che provengono dai sensori Hall consentono, una volta decodificati, di determinare la posizione del rotore e sincronizzare con essa la corretta sequenza di commutazione delle fasi.
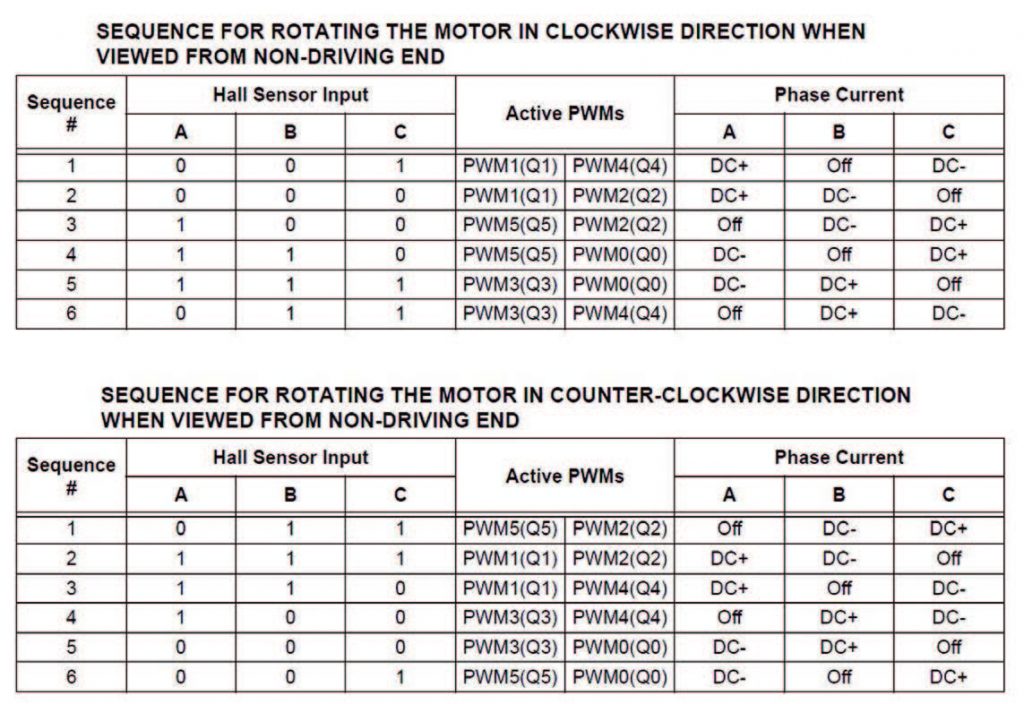
Tabella 1: Sequenze di commutazione del driver del circuito di controllo
Tali sensori sono posizionati in maniera tale da essere spostati di 60° o 120° l’uno rispetto all’altro e necessitano di alimentazione, tipicamente una tensione compresa tra 4 e 24 Volt e corrente di poche decine di milliampere. L’uscita dei circuiti a sensori Hall è normalmente costituita da transistor in configurazione a collettore aperto, ai quali è necessario aggiungere delle resistenze di pull-up dal lato controller per fruire dell’informazione. In Figura 3 è mostrato lo schema a blocchi di questa logica di controllo.
Nota: I sensori Hall basano il loro funzionamento sul cosiddetto Effetto Hall. Se una corrente attraversa un conduttore immerso in un campo magnetico, questo esercita una forza trasversale sulle cariche in movimento che tende ad addensare le cariche stesse su di un lato del conduttore. Tra le due facce estreme del conduttore si origina di conseguenza una d.d.p. misurabile. La scoperta del fenomeno risale al 1879 ad opera di Edwin Herbert Hall.
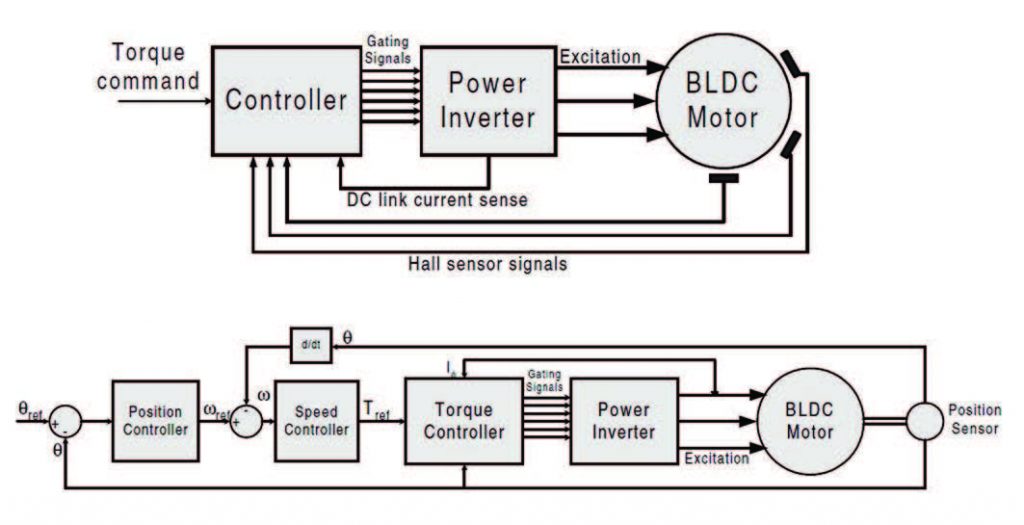
Figura 3: Schema generale a blocchi di controllo di un motore BLDC e di un servomeccanismo di posizione impiegante un motore BLDC

Figura 4: Un motore BLDC a tre fasi presenta normalmente tre sensori Hall montati sullo statore sul lato opposto a quello dal quale è fruibile la coppia motrice
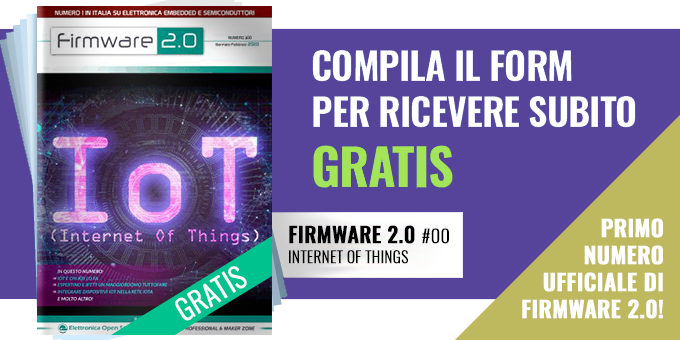
Tali sensori possono muoversi di 60° o 120° l’uno dall’altro e richiedono normalmente una tensione di 4 a 24 Volt e una corrente di poche decine di milliampere. I transistor in configurazione a collettore aperto costituiscono tipicamente l’uscita dei circuiti a sensori Hall, ma per utilizzare l’informazione, è necessario aggiungere resistenze di pull-up dal lato del controller. Lo schema a blocchi di questa logica di controllo è rappresentato nella Figura 3.