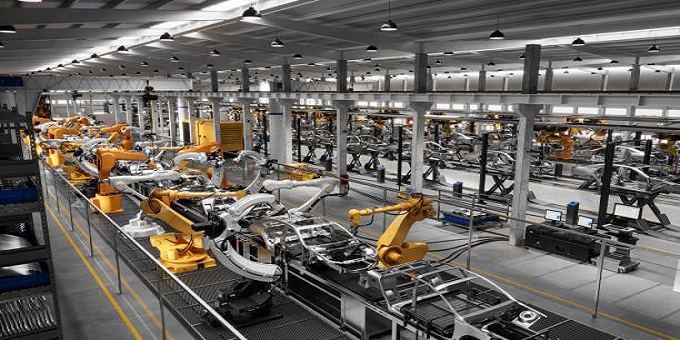
Sul blog di Elettronica Open Source puoi leggere non solo tutti gli articoli Premium riservati agli abbonati Platinum 2.0 e inseriti nella rivista Firmware 2.0 (insieme ad articoli tecnici, progetti, approfondimenti sulle tecnologie emergenti, news, tutorial a puntate, e molto altro) ma anche gli articoli della Rubrica Firmware Reload. In questa Rubrica del blog abbiamo raccolto gli articoli tecnici della vecchia rivista cartacea Firmware, che contengono argomenti e temi evergreen per Professionisti, Makers, Hobbisti e Appassionati di elettronica. A tutti coloro che operano nel settore dell’automazione è capitato di sentire il termine “Industry 4.0”, espressione alla moda coniata nel 2011 alla fiera di Hannover. Questa visione dell’industria immagina che le fabbriche di domani saranno molto più integrate, automatizzate e flessibili. I nuovi stabilimenti, più veloci ed efficienti, sforneranno tutte le merci richieste da mercati in trasformazione.
Introduzione
L’espressione “Industry 4.0” presuppone l’idea che il mondo abbia già attraversato tre rivoluzioni industriali e che si trovi ora alla vigilia della quarta (Figura 1, Nota 1).
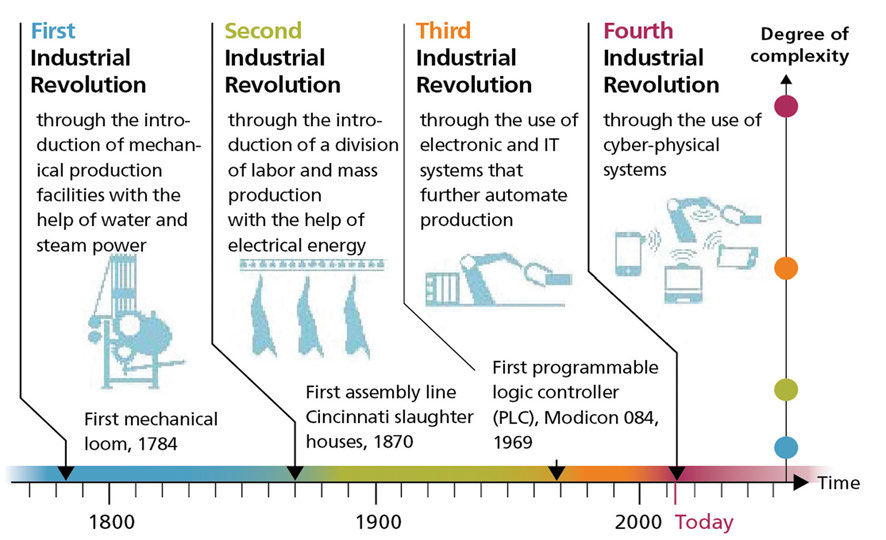
Figura 1: Dal passato ai giorni nostri, possiamo identificare quattro diversi momenti chiave nell’evoluzione dell’automazione industriale. Fonte del grafico: DFKI
La quarta, odierna rivoluzione dell’automazione manifatturiera e di processo sarà basata, ovviamente, su sistemi connessi: sensori, attuatori e sistemi di controllo, collegati per mezzo di diversi tipi di reti tramite il protocollo Internet. Portando nel cloud i dati provenienti dalle macchine e dai sensori, diviene possibile svolgere analisi molto utili per ottimizzare la produzione, prevedere i guasti, pianificare la manutenzione, rifornire automaticamente i magazzini e perfino personalizzare le specifiche del prodotto finito in funzione delle dinamiche di mercato. Un esempio di Industry 4.0 molto interessante ed attuale è rappresentato dal nuovo stabilimento statunitense di General Electric, situato a Schenectady, nello stato di New York. Questa fabbrica di batterie sodio-nichel è dotata di oltre 10.000 sensori, sparsi su uno spazio produttivo di oltre 16 mila metri quadrati, tutti collegati ad una rete Ethernet interna ad alta velocità (Nota 2). Come scrive la MIT Technology Review: “[I sensori] monitorano aspetti relativi alla tracciabilità dei lotti di materiale usato per fabbricare la ceramica contenuta nelle batterie, la temperatura utilizzata per cuocerla, l’energia necessaria per fabbricare ciascuna batteria, perfino la pressione dell’aria. I dati vengono raccolti tramite nodi Wi-Fi allestiti in tutta la fabbrica, da addetti equipaggiati con iPad.” (Nota 3). Questo articolo parte dal presupposto che la quarta rivoluzione industriale sia già in corso. Sostiene, inoltre, che la connettività onnipresente all’interno degli stabilimenti porterà ad aumenti di produttività e predicibilità ottenuti principalmente grazie a software e algoritmi sempre più efficaci. Sì, è una visione impressionante, ma anche realizzabile. Prima di costruire la necessaria infrastruttura e quindi avviare effettivamente questa rivoluzione, occorre però superare vari ostacoli progettuali a livello di sistema. Questo articolo ne esamina alcuni.
Considerazioni progettuali sistemiche per Industry 4.0
La realizzazione della visione di Industry 4.0 si protrarrà probabilmente per uno o due decenni, ma sta già avendo effetti sui progetti di numerosi sistemi. L’automazione in Figura 2 illustra i tre aspetti fondamentali che devono essere implementati nei progetti dei sistemi per realizzare Industry 4.0.
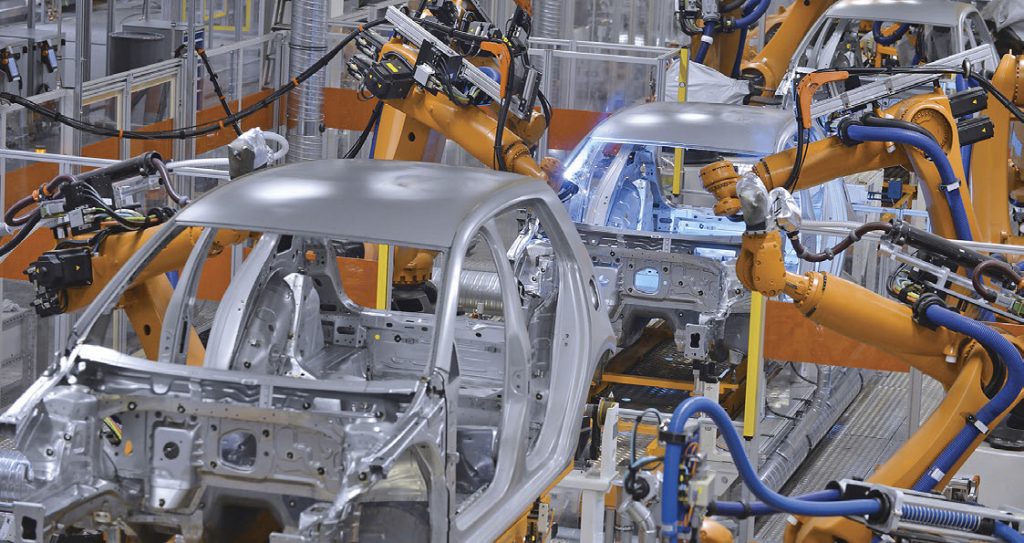
Figura 2: Industry 4.0 impone ai sistemi industriali tre requisiti fondamentali: elaborazione e controllo distribuiti, sensoristica pervasiva e sistemi autenticati e sicuri
ELABORAZIONE E CONTROLLO DISTRIBUITI
Una tendenza fondamentale a livello di sistema, già in atto, riguarda l’ubicazione delle risorse di elaborazione e controllo. È infatti necessario un controllo distribuito per rendere flessibili le linee di assemblaggio complesse, ridurre la latenza del controllo stesso ed alleggerire i requisiti di elaborazione che gravano sul PLC principale. Tutto questo sarà ancora più comune nelle fabbriche della prossima generazione. I PLC diventeranno sempre più piccoli e gestiranno un numero sempre maggiore di canali I/O, analogici e digitali. Dovranno inoltre utilizzare una varietà di protocolli I/O, compresi i più recenti come lo standard IO-Link®.
SENSORISTICA PERVASIVA
Quali tendenze riguardano i sensori? La premessa fondamentale di Industry 4.0 è la condivisione dei dati di produzione, ma ciò significa in primo luogo che occorre raccogliere una quantità di dati sempre più grande. Questa valanga di informazioni è dovuta all’enorme diffusione dei sensori all’interno della fabbrica (o dell’impianto di processo), così come nei siti remoti. Anche se oggi un determinato parametro di processo non influisce sull’algoritmo di controllo, i relativi dati devono comunque essere raccolti per un probabile uso futuro. Possiamo attenderci che, grazie ai progressi previsti nel campo degli algoritmi sul cloud, un domani diverrà possibile “reinventare” vecchi parametri di processo per prevedere importanti guasti del sistema. Spesso per indicare la crescente diffusione dei sensori si usa l’espressione “sensoristica pervasiva”. Torneremo su questo argomento in seguito.
SICUREZZA AUTENTICATA
Infine, il collegamento di tutti i sensori, sistemi di controllo e attuatori tramite il protocollo Internet - per consentire l’analisi dei “big data” - aumenta decisamente le preoccupazioni riguardanti la sicurezza informatica. Gran parte dei problemi di sicurezza nel mondo industriale sono affrontati tramite firewall software e switch/gateway Internet sicuri. Ma le preoccupazioni riguardanti la sicurezza vanno oltre questi portali di comunicazione e raggiungono l’hardware. I nuovi standard di “difesa in profondità” (defense-in-depth) richiedono infatti che la rete dei dispositivi finali (ad esempio sensori e PLC, in questo contesto) sia autenticata e sicura. I requisiti di sicurezza ad ampio spettro, comprendenti software e hardware, hanno effetti diretti sui progetti a livello di sistema.
CONTROLLO DISTRIBUITO E LOCALE: L’ASCESA DEL MICRO-PLC
La disponibilità di PLC più piccoli ma ugualmente potenti, che consentano il controllo distribuito e locale dei processi o delle linee di assemblaggio, è un obiettivo ambito ai fini della riduzione della latenza. Ma, per progettare un micro-PLC occorre affrontare difficili sfide tecniche sul fronte dell’integrazione degli I/O analogici e della dissipazione di calore. Queste sfide sono state superate con successo nel progetto "prova di concetto" (proof-of-concept) di Micro PLC sviluppato da Maxim (Figura 3).
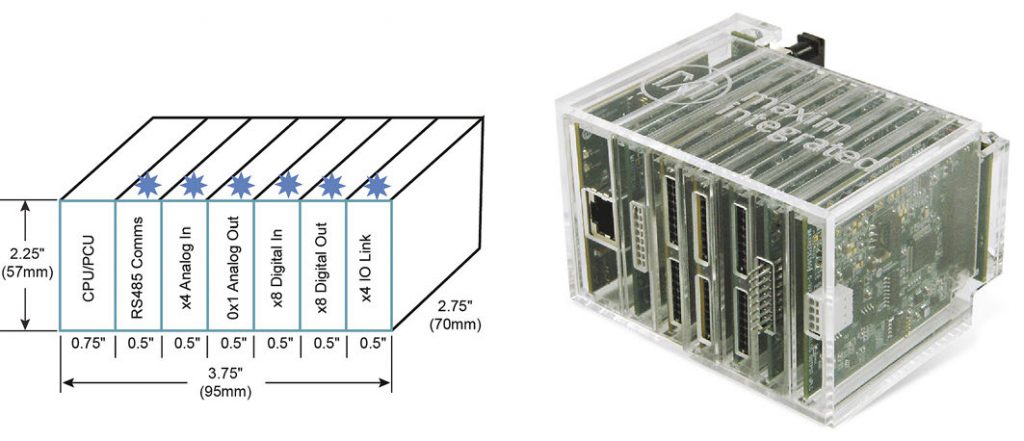
Figura 3: Questa “prova di concetto” di un Micro PLC integra un microcontrollore a 32 bit, connettività Ethernet e 25 canali di I/O. Il volume totale è di 406.125 mm3
Il Micro PLC di Maxim, che può essere contenuto nel palmo di una mano, integra un microprocessore a 32 bit e la necessaria connettività Ethernet, e gestisce in tutto 25 canali di I/O. In particolare, il sistema offre:
- Quattro canali d’ingresso ed un canale d’uscita analogici
- Otto canali d’ingresso e otto canali d’uscita digitali
- Un modulo IO-Link quadruplo che si interfaccia con quattro sensori abilitati IO-Link
- Efficace integrazione analogica
È noto che nei moduli di I/O dei PLC i componenti analogici e discreti occupano dal 50% al 70% della scheda. È altresì noto che questi stessi moduli costituiscono la parte più ingombrante di tutti i PLC. Ne consegue che per ridurre un completo sistema PLC ad un formato così piccolo occorre vincere la sfida dell’integrazione analogica degli I/O. Un modo per raggiungere questo obiettivo consiste nell’utilizzare dispositivi analogici integrati al posto di numerosi componenti discreti, spesso centinaia di essi. Così facendo, le dimensioni della scheda si riducono, il consumo di potenza diminuisce e l’affidabilità aumenta. La Figura 4 presenta un serializzatore ottale (MAX31911) ed un isolatore dati a quattro canali (MAX14932) utilizzati per sostituire decine di optoisolatori discreti e centinaia di resistori e condensatori, presenti nel progetto tradizionale a sinistra.
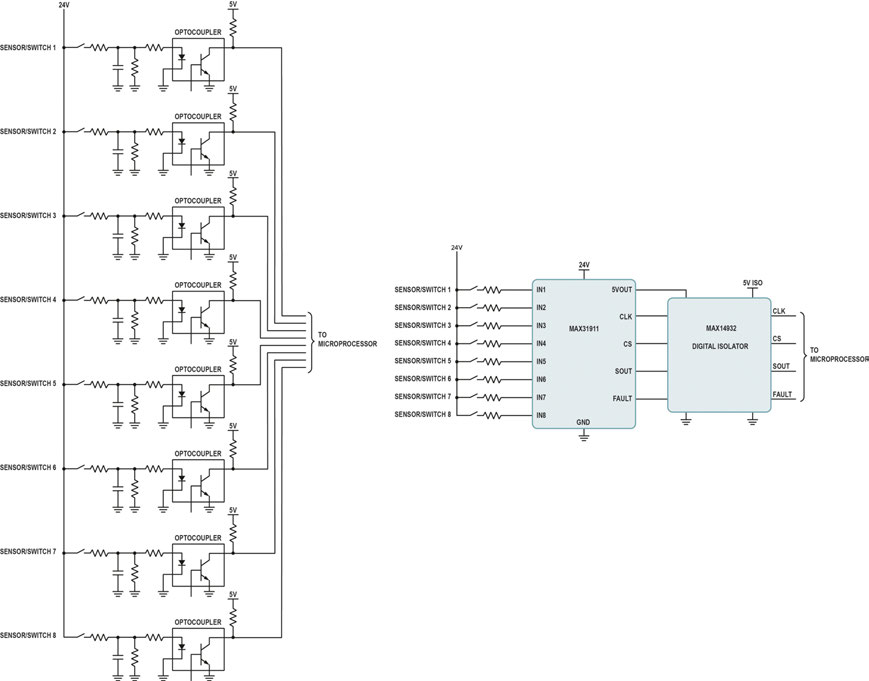
Figura 4: In questa “prova di concetto” di un Micro PLC, due chip sostituiscono centinaia di componenti discreti
Con questa soluzione compatta, il Micro PLC ha la stessa capacità di canali I/O di un PLC normale. Dissipazione di calore ed efficiente conversione di potenza. Integrando così tanti canali in un formato così piccolo, la dissipazione di calore e l’efficienza della conversione di potenza - relativa al convertitore a commutazione DC-DC presente sulla scheda - divengono problemi importanti. Un’efficienza più alta comporta temperature di funzionamento molto più basse. La Figura 5 mostra l’andamento dell’efficienza di conversione per il regolatore a commutazione sincrono DC-DC MAX17505 nell’erogazione di diversi valori di corrente di carico, con un’uscita di 5 V.
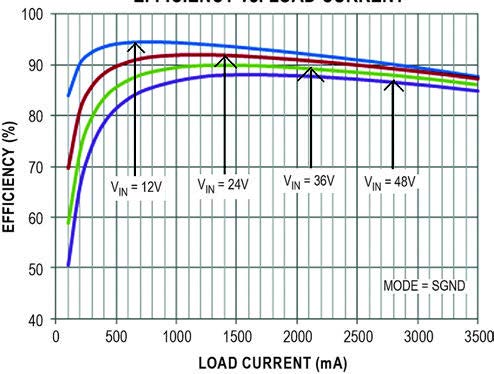
Figura 5: Efficienza in funzione della corrente di carico. I dati mostrano un’efficienza superiore al 90% per un’ampia gamma di valori di VIN e corrente di carico
Grazie ad un’efficienza superiore al 90% (con tensione di ingresso del backplane di 24 V e corrente superiore ad 1 A), questa famiglia di regolatori di tensione opera a temperature inferiori dal 30% al 50% rispetto a soluzioni precedenti. Ciò si traduce in una generazione di calore nettamente inferiore, che facilita l’integrazione di numerosi moduli I/O in un piccolo Micro PLC. Le caratteristiche del convertitore step-down a rettificazione sincrona MAX17505, caratterizzato da alta efficienza ed alta tensione, meritano un approfondimento (Figura 6).
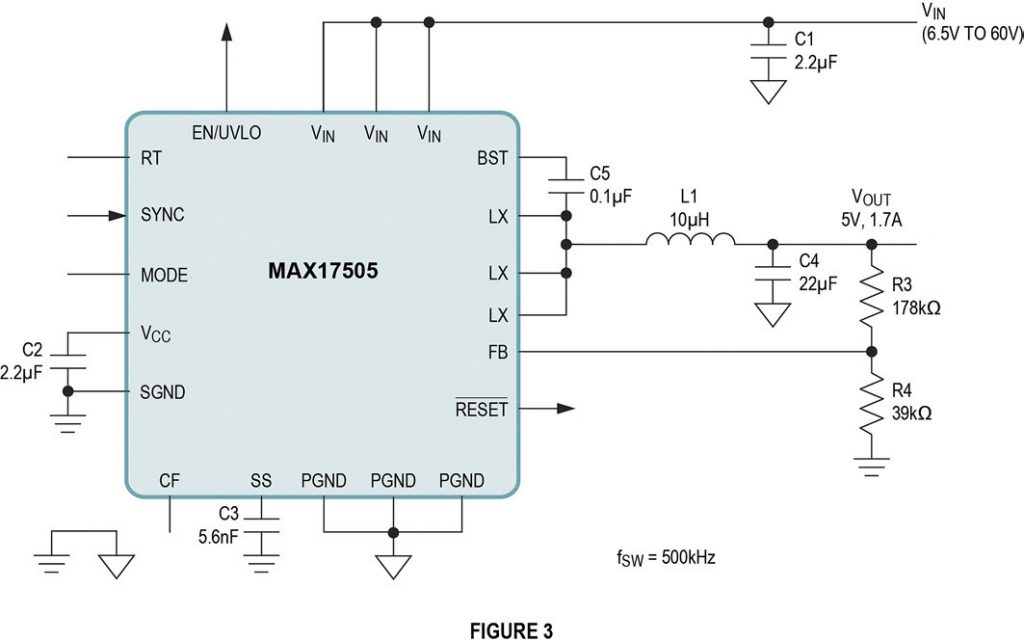
Figura 6: Il convertitore step-down a rettificazione sincrona MAX17505, ad alta efficienza ed alta tensione, è dotato di due MOSFET integrati. Accetta tensioni di ingresso comprese tra 4,5 V e 60 V ed eroga una corrente massima di 1,7 A con una tensione d’uscita compresa tra 0,9 V e il 90% di VIN
Dotato di due MOSFET integrati, accetta in ingresso tensioni comprese tra 4,5 V e 60 V ed eroga una corrente massima di 1,7 A, con una tensione d’uscita compresa tra 0,9 V e il 90% di VIN. Grazie alla compensazione incorporata per l’intera gamma di tensione d’uscita, può fare a meno di componenti esterni; offre inoltre una precisione di ±1,1% nella regolazione feedback (FB), per temperature comprese tra -40°C e +125°C. Il dispositivo è dotato di un contenitore TQFN senza piombo di dimensioni ridotte (4 mm x 4 mm), con una piazzola esposta. Sono disponibili modelli di simulazione. Il MAX17505 impiega un’architettura di controllo basata sulla modalità a corrente di picco, con una funzione MODE che consente di scegliere tra diverse modalità di funzionamento: modulazione della durata degli impulsi (PWM), modulazione della frequenza degli impulsi (PFM), o modalità a conduzione discontinua (DCM). La modalità PWM assicura un funzionamento a frequenza costante per tutti i valori di carico, ed è utile in applicazioni sensibili alla frequenza di commutazione. La modalità PFM disabilita la corrente negativa dell’induttore e consente di “saltare” alcuni impulsi, ai bassi valori di carico, per aumentare l’efficienza. La modalità DCM, che impiega una frequenza costante ed è utilizzata per valori di carico ancora più bassi, non consente di “saltare” impulsi ma si limita a disabilitare la corrente negativa dell’induttore. La DCM offre valori di efficienza intermedi tra la PWM e la PFM. I MOSFET a bassa resistenza integrati nel chip assicurano alta efficienza a pieno carico e semplificano il layout.
Sensoristica pervasiva con lo standard di comunicazione IO-Link
Nelle fabbriche di domani i sensori saranno onnipresenti e - connessi ai gateway o direttamente ai PLC tramite varie interfacce - non si limiteranno più ad inviare semplici segnali ON/OFF, ma trasmetteranno una ricca varietà di dati. Qui emerge l’importanza del protocollo IO-Link, una tecnica di comunicazione da sensori che si sta diffondendo molto rapidamente. IO-Link è uno standard IEC®, ma è basato sull’affermato sistema a tre fili per la connessione di sensori e attuatori. A partire dagli anni ottanta, i bus di campo industriali hanno permesso di ottenere dispositivi più intelligenti ed installazioni più rapide, semplificando i cablaggi e la manutenzione. Tuttavia, la mancanza di un singolo bus di campo universalmente accettato ha anche creato confusione, difficoltà nella formazione dei tecnici, costi elevati, problemi di compatibilità tra gli apparati. Il protocollo IO-Link è il primo standard aperto di comunicazione seriale punto-punto, rivolto a sensori e attuatori, indipendente da specifici bus di campo e al contempo economico. È stato inoltre adottato come standard internazionale (IEC 61131-9), vedi Nota 4. Il protocollo IO-Link standardizza l’interoperabilità tra apparati industriali di tutto il mondo. Questo standard può essere implementato direttamente nel PLC o integrato in qualunque bus di campo. Grazie alla propria flessibilità, IO-Link sta rapidamente diventando lo “standard di fatto” per la comunicazione universale con dispositivi intelligenti come il sensore di luce Santa Cruz di Maxim, il MAXREFDES23# (Figura 7).
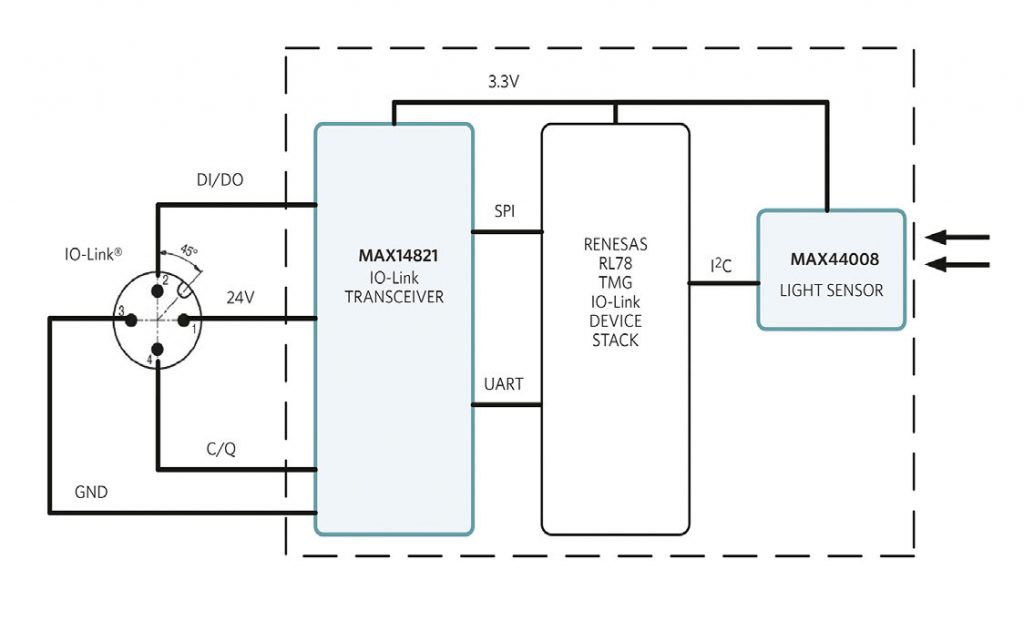
Figura 7: Schema a blocchi del progetto di riferimento Santa Cruz, un sensore di luce
La tecnologia IO-Link, insieme alla continua miniaturizzazione dei dispositivi, facilita il dispiegamento di sensori piccolissimi e a basso consumo in tutta la fabbrica. La Figura 8 mostra il sensore di luce Santa Cruz, dotato di interfaccia IO-Link. Il sistema Santa Cruz MAXREFDES23#, uno dei sensori di luce IO-Link più piccoli al mondo, integra sei diversi sensori - per il rilevamento di luce ambientale (bianca), rossa, verde, blu, infrarossi e temperatura - in una piccola scheda a circuito stampato (PCB).
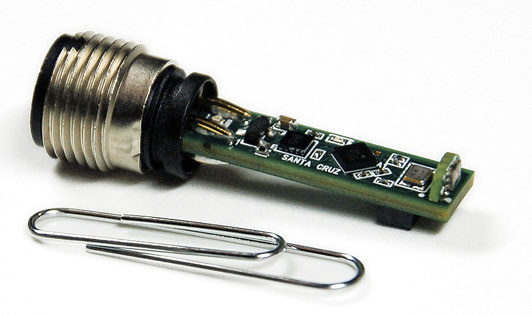
Figura 8: Il MAXREFDES23#, un piccolo sensore di luce IO-Link, integra sei sensori diversi per il rilevamento di luce ambientale (bianca), rossa, verde, blu, infrarossi e temperatura. Il tutto in una piccola scheda a circuito stampato (PCB) di 6,5 mm x 25 mm
Il progetto Santa Cruz comprende un transceiver Maxim conforme allo standard industriale IO-Link (MAX14821); un microcontrollore Renesas® Electronics a 16 bit a bassissimo consumo (RL78) che impiega il device stack IO-Link della società TMG TE (Technologie Management Gruppe Technologie und Engineering); ed un sensore di luce Maxim MAX44008 (Figure 7 e 8). La collaborazione tra queste aziende ha permesso di realizzare un progetto di riferimento per sensore di luce conforme alla versione 1.1/1.0 di IO-Link. Dispositivi compatti come il Santa Cruz facilitano l’impiego di molti sensori per raccogliere dati utili e inviarli, tramite il protocollo IO-Link, a un concentratore collegato al cloud o ad un PLC. Gli odierni sensori industriali come il Santa Cruz devono essere estremamente efficienti dal punto di vista energetico, poiché sono piccoli e racchiusi in un contenitore ai fini della sicurezza. Sempre più spesso, pertanto, questi sensori impiegano regolatori DC-DC a commutazione ad alta efficienza, al posto dei tradizionali LDO. Prodotti come il regolatore DC/DC di Maxim illustrato in Figura 9 sono progettati per assicurare un’efficienza superiore al 90% anche quando erogano correnti di carico di soli 25 mA o 50 mA.
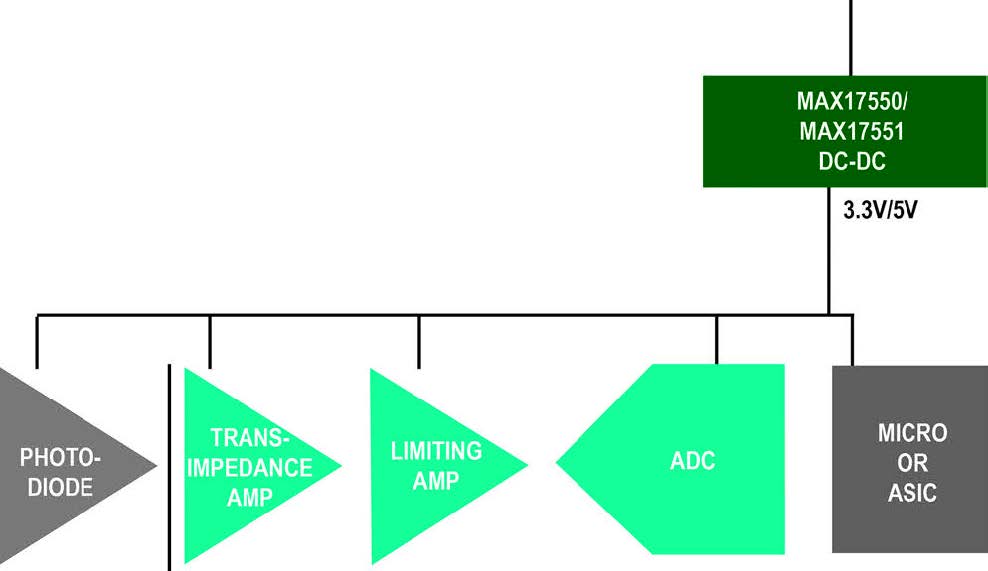
Figura 9: Il regolatore a commutazione DC-DC ad alta efficienza MAX17550/MAX17551 è progettato per erogare basse correnti di carico nelle applicazioni sensoristiche
LA NECESSITÀ DI SICUREZZA PER L’HARDWARE EMBEDDED
Non è un segreto che non sempre i produttori di IC attribuiscano alla sicurezza informatica un’importanza critica. Risultati simili sono emersi anche da un recente sondaggio a cui hanno partecipato 599 tra responsabili IT e responsabili della sicurezza IT di tredici paesi, sponsorizzato da Unisys “in partnership con il Ponemon Institute”. Lo studio ha rilevato che solo il 28% degli interpellati considera la sicurezza come una delle cinque priorità strategiche per la propria azienda. Quasi il 60% delle stesse persone, però, ha ammesso che le minacce informatiche rappresentano un rischio per i sistemi di controllo ed i sistemi SCADA (vedi Nota 5). Solo il 28% degli interpellati, dunque, ritiene che la sicurezza informatica sia una priorità. Un dato inquietante, se si considera che il controllo distribuito e l’onnipresente connettività determinano già oggi un maggiore bisogno di sicurezza. Una necessità a cui si risponde principalmente migliorando i firewall ed i sistemi di rilevamento delle intrusioni e con architetture di switching più sicure. Ma altrettanto importante è disporre di un hardware fidato, soprattutto nel caso dei moduli di I/O e dei sensori remoti sul campo. Questi dispositivi possono infatti essere clonati o manomessi, soprattutto se scarsamente protetti dal punto di vista fisico. Violazioni di questo tipo compromettono seriamente l’infrastruttura chiamata a prendere decisioni critiche sulla base dei dati raccolti dai sensori. Di conseguenza, è fondamentale assicurare che questi sistemi siano autenticati e sicuri. In definitiva, senza un hardware embedded sicuro non potremo sfruttare a pieno il potenziale di Industry 4.0. La sicurezza informatica dei sistemi per Industry 4.0 inizia dai sensori che inviano dati al cloud o al PLC. Ogni eventuale violazione a questo livello può avere gravi conseguenze. Se, ad esempio, la manomissione di un sensore provocasse l’invio di dati fasulli sul livello di petrolio in un serbatoio o sulla pressione in una conduttura, le azioni compiute (o non compiute) in base a quei dati potrebbero avere conseguenze catastrofiche. È una visione troppo drammatica? Niente affatto. Ovviamente, i dati forniti da sensori inaffidabili possono causare anche conseguenze meno catastrofiche, seppure gravi. Ad esempio, possono rendere del tutto inutili i programmi di analisi dei “big data” che usano i dati dei sensori per pianificare la manutenzione. La posta in gioco è la disponibilità degli impianti, la manutenzione predicibile, l’efficienza industriale complessiva: in altri termini, i fondamenti stessi di Industry 4.0. Garantire costantemente la sicurezza fisica di tutti i sensori può risultare impossibile, soprattutto nel caso di installazioni remote come quella di Figura 10, usata per monitorare un impianto di estrazione di petrolio e gas naturale. La difficoltà nel limitarne l’accesso rende questi sensori vulnerabili agli attacchi fisici, pertanto è essenziale provvedere ad una loro autenticazione prima di accettarne i dati.
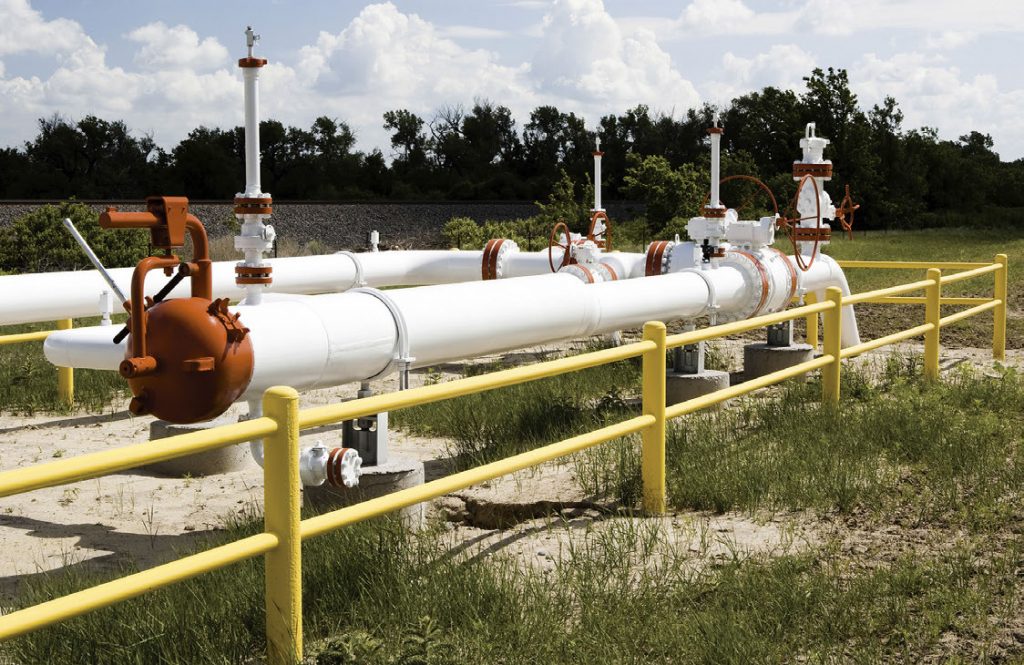
Figura 10: I sensori remoti sono particolarmente vulnerabili agli attacchi fisici ed alle violazioni della sicurezza. I metodi di autenticazione sicura eliminano i falsi positivi e le informazioni di stato imprecise
Fortunatamente, da anni esiste un metodo di autenticazione efficace, ideato per i dispositivi medici e per prodotti consumer come le cartucce delle stampanti. Le odierne tecniche di autenticazione sono perlopiù basate su standard e devono essere implementate con dispositivi a prova di manomissione conformi al protocollo di autenticazione. La Figura 11 illustra lo schema a blocchi concettuale di un metodo di autenticazione basato su hardware che impiega l’algoritmo simmetrico SHA-256. Il protocollo SHA-256, basato su uno scambio interrogazione-risposta tra dispositivi autorizzati, autentica il sensore prima che i suoi dati siano accettati e letti. L’autenticazione SHA-256 rende impossibile per l’aggressore collegarsi alla rete fingendo di essere un sensore, così come sostituire il sensore originale con un dispositivo contraffatto (vedi Nota 6).
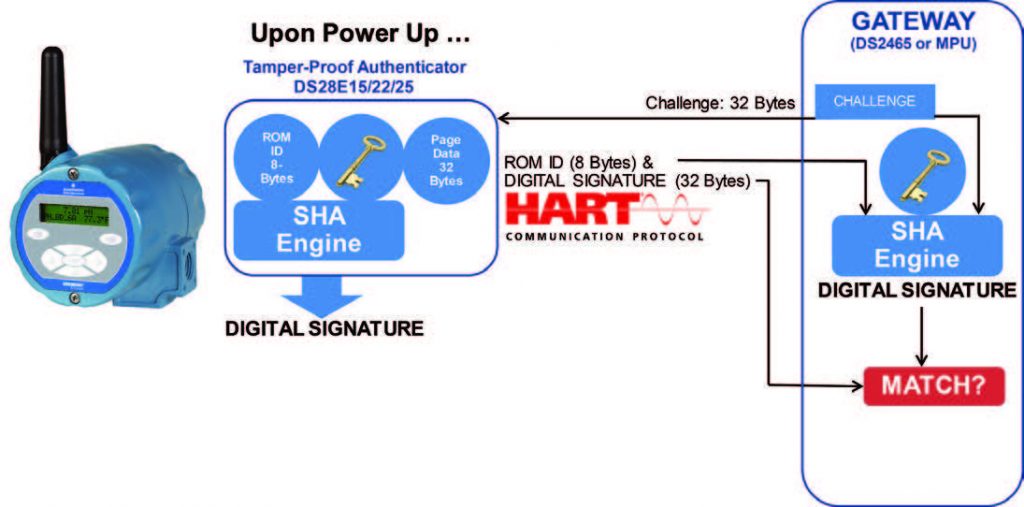
Figura 11: Autenticazione basata su SHA-256 per sensori remoti sul campo, con protocollo HART o con qualunque altro standard di comunicazione. I dati della pagina (32 byte) e la chiave (2 byte) sono noti sia al sensore sia all’host. Il tutto con un piccolo aumento del numero di byte trasmessi. HART® è un marchio registrato della HART Communication Foundation. L’immagine del trasmettitore wireless è stata gentilmente fornita da Emerson Process Management
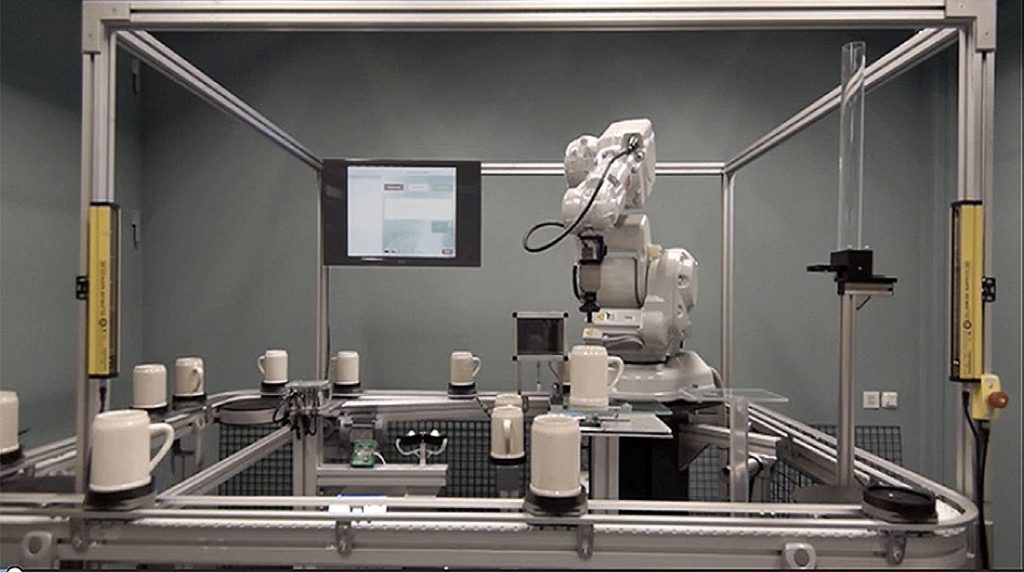
Figura 12: Sistema di incisione su tazze completamente robotizzato, nel quale si fa largo uso di sensoristica Maxim Integrated
CONCLUSIONI
L’espressione Industry 4.0 è utilizzata oggi per descrivere gli stabilimenti manifatturieri interconnessi, dove i dati provenienti da una varietà di PLC distribuiti, sensori ed altri dispositivi di campo sono aggregati per poter sfruttare i vantaggi offerti dai software di analisi ed ottimizzazione. Industry 4.0 promette di ottimizzare gli asset produttivi in termini di disponibilità, manutenzione programmata, efficienza energetica ed uso efficiente di tutte le risorse. I dati di produzione possono inoltre essere integrati nel software ERP e CRM dell’azienda per pianificare i processi produttivi in modo efficiente, o addirittura per personalizzare i prodotti modificando i parametri delle linee di assemblaggio e dei processi. Per rendere interconnessi i sistemi produttivi, di qualunque tipo essi siano, occorre però considerare vari importanti fattori di progetto a livello di sistema. Alcuni di essi sono stati esaminati in questo articolo. Abbiamo mostrato come alcune delle sfide riguardanti i sistemi industriali possano essere affrontate tramite nuovi componenti a semiconduttore, soprattutto nel dominio analogico/mixed-signal. Queste nuove tecnologie integrate permettono non solo di rimpicciolire i sensori ed i PLC, ma anche di aumentare in modo economico la sicurezza embedded di alcuni dispositivi critici di I/O dislocati sul campo. La transizione verso Industry 4.0 richiederà indubbiamente ulteriori considerazioni riguardanti la progettazione dei sistemi destinati alle fabbriche. Sfruttando le tecnologie più recenti potremo raggiungere gli obiettivi prefissati in termini di consumi, prestazioni e funzioni di comunicazione.
Articolo della rivista cartacea Firmware Anno 2015 - Numero 112
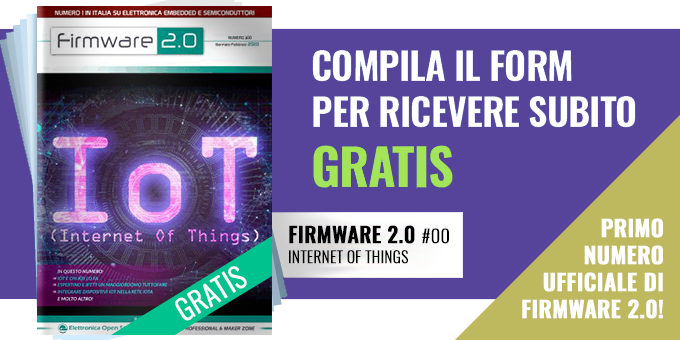